Detailed Report
OEM Manufacturing
OEM (Original Equipment Manufacturer) manufacturing involves producing components or products that are later integrated into another company’s end product. It enables companies to specialize and streamline production processes efficiently.
Introduction
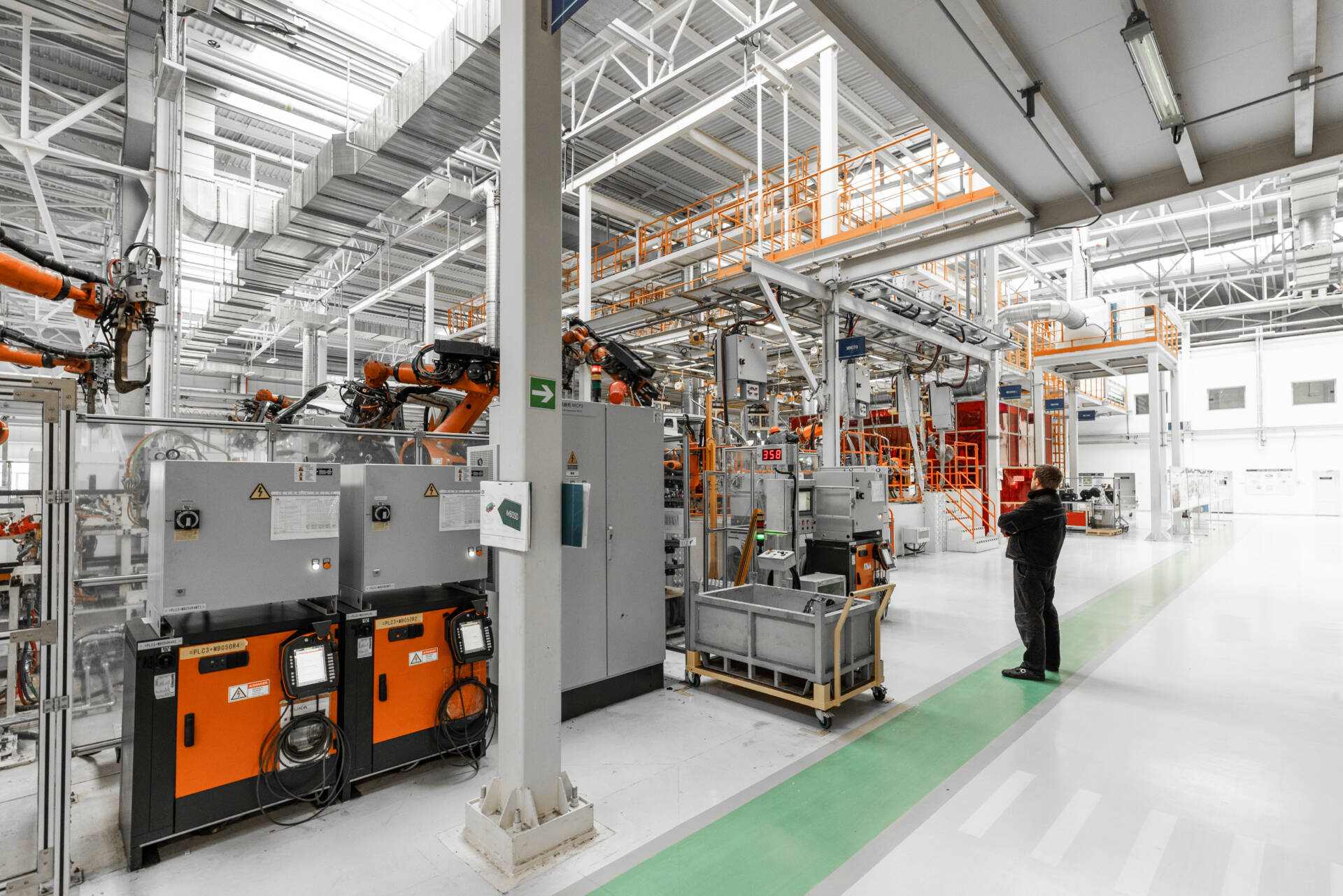
Detailed Report on OEM Manufacturing is as follows.
In the past, an original equipment manufacturer (OEM) was a corporation that supplied equipment to another company for them to resell or put in their own equipment for sale. The word “OEM” now refers to a product that a company purchases to resell or mix with another product under the reseller’s brand name. OEM is sometimes used to identify a company that manufactures the finished product using components from another manufacturer.
Original equipment manufacturer software is software that comes pre-installed with new computers or other goods. It can also refer to the practice of acquiring huge quantities of commercial software and reselling it later, typically combined with other commodities. Furthermore, this type of software is intended for use with physical components. It is provided by the same company that created the system or equipment; it lacks a separate brand identification. OEM software is occasionally perceived to be less efficient than its equivalent; however, this relies on the grade of the program and if it was built for a specific use.
Before selling a product to end users, companies assess the most effective technique for meeting client demands. They consider a variety of options while determining whether to buy, create, develop, or cooperate with someone else to design the answer. Collaboration with OEMs allows a firm to shorten the product life cycle, obtain product design knowledge, and reduce manufacturing expenditure. Costs of production and materials can also be decreased. Companies may still build products with best-in-class components while remaining focused on their core strengths.
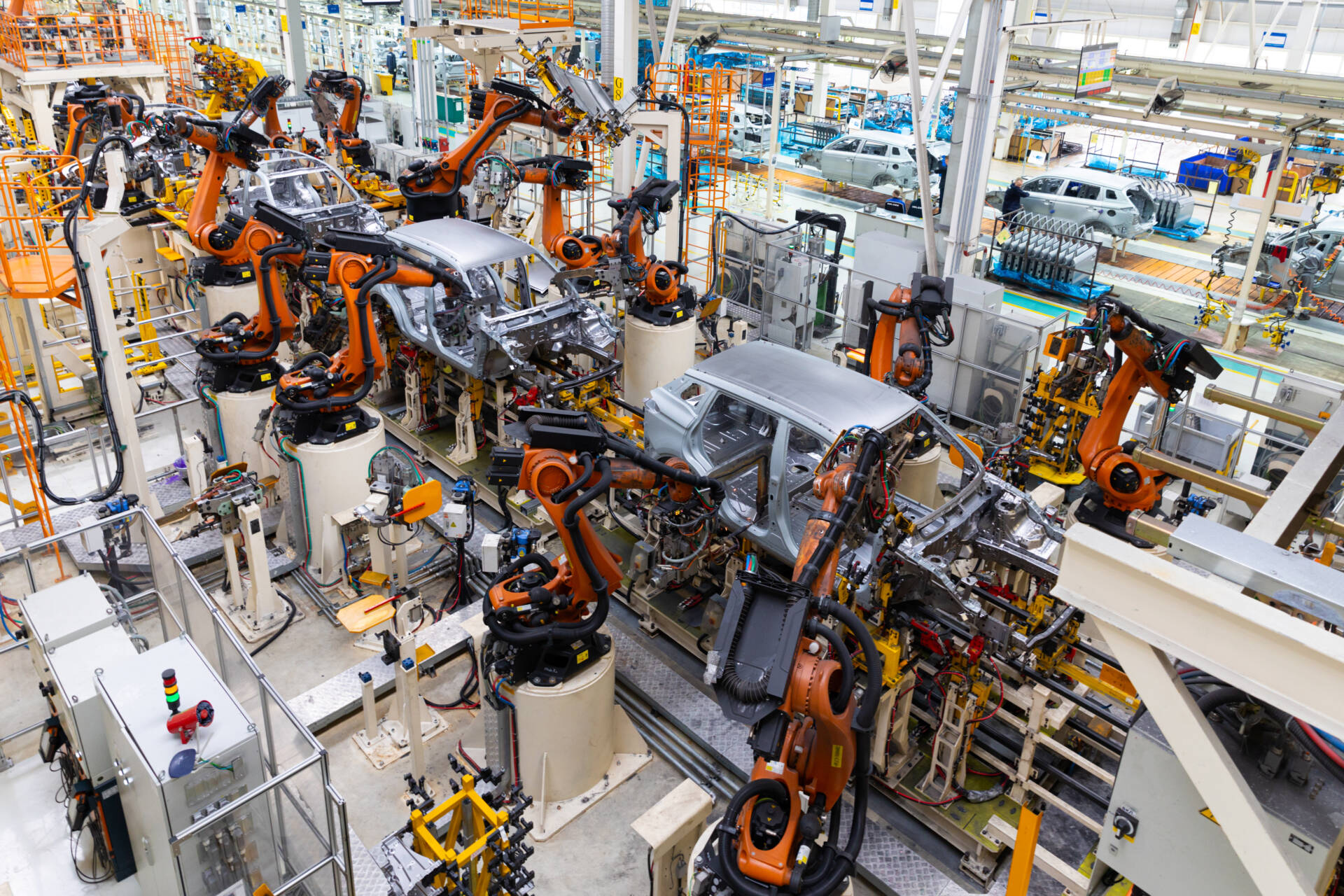
Detailed Report Sample On OEM Manufacturing
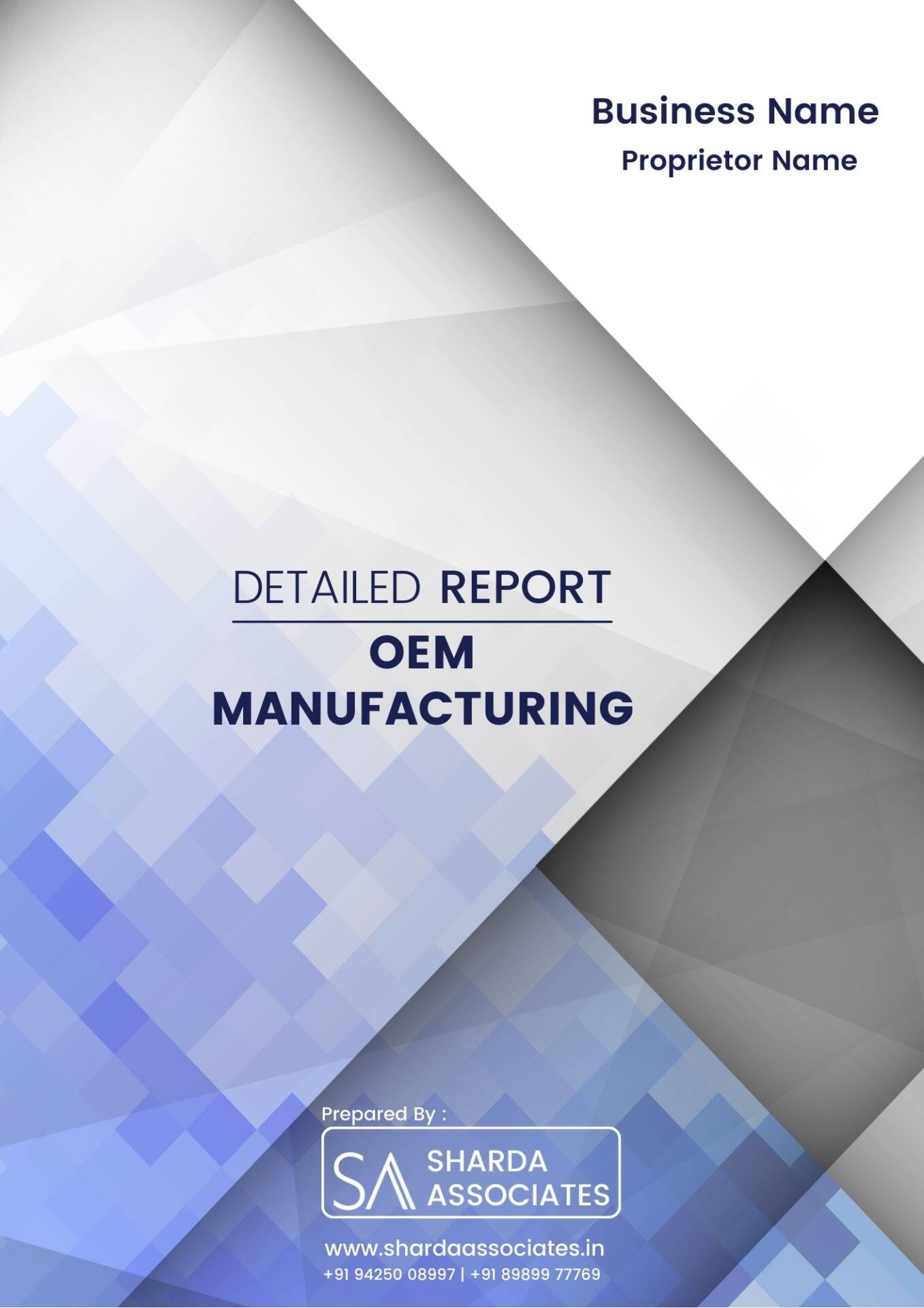
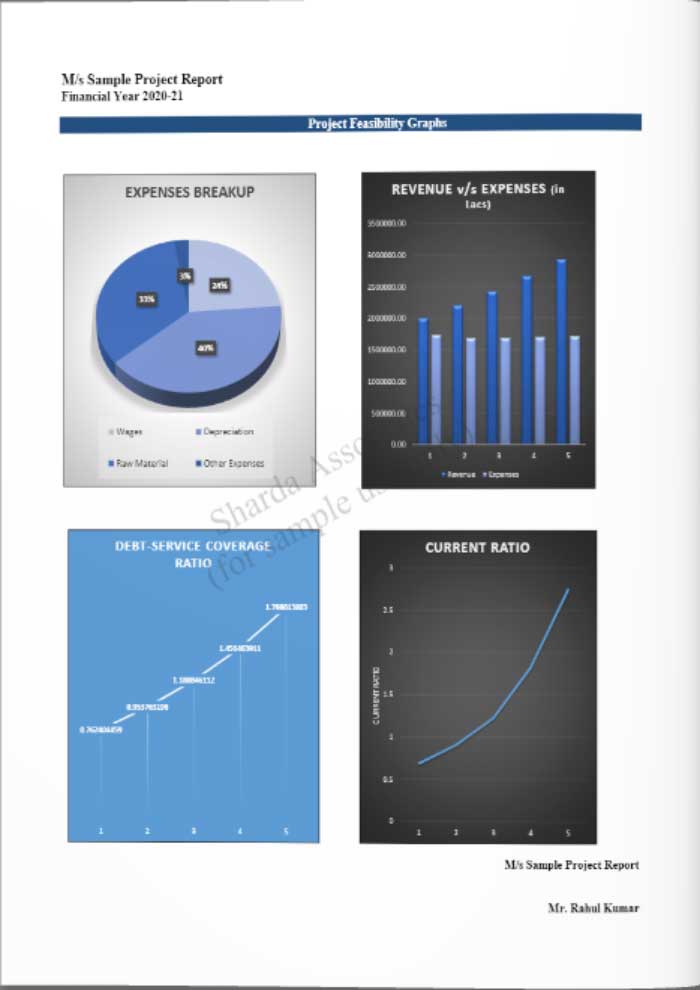
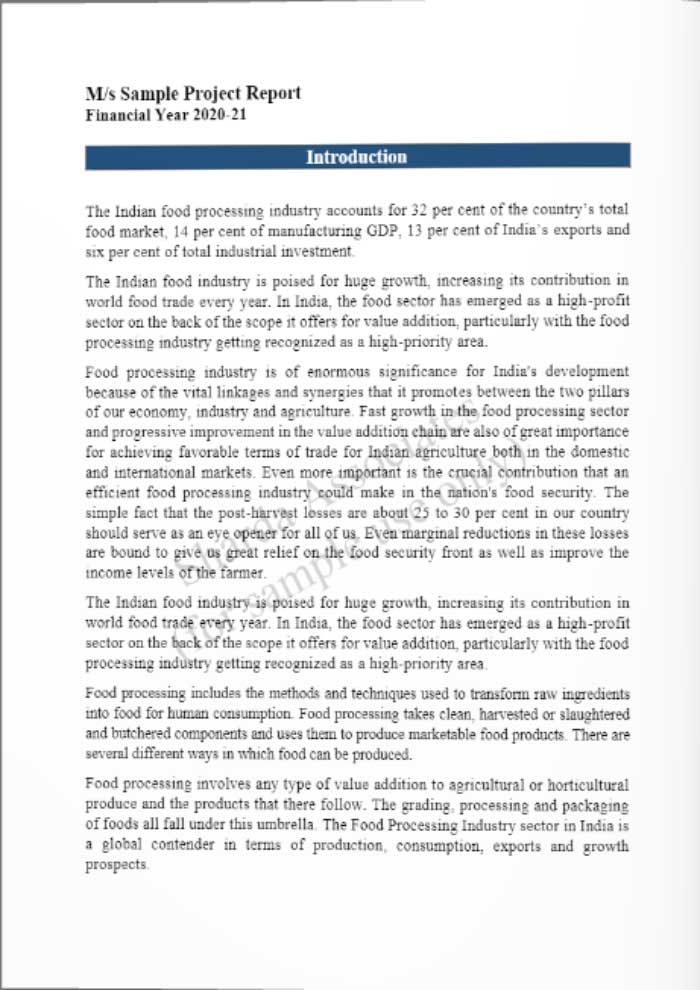
Market Potential Of OEM Manufacturing
The worldwide automotive OEM market is predicted to grow at a CAGR of 4.17% on average. In 2023, the market is anticipated to be valued US$35.16 billion. The vehicle OEM business is predicted to have risen to a value higher than US$ 52.90 billion by 2033.
The market potential for OEM manufacturing is strongly tied to the need for production outsourcing. Many firms choose to outsource manufacturing to specialized OEM suppliers in order to save costs, focus on core competencies, and get access to specialized knowledge. The OEM manufacturing industry has grown as a result of the prevalent trend of outsourcing manufacture to countries with cheaper labor costs, such as China and India. The development prospects of sectors that rely on OEM manufacturing may have an influence on market potential. Automotive, electronics, telecommunications, and medical equipment, for example, rely heavily on OEM manufacturing to meet their production demands. If these industries grow significantly, the demand for OEM manufacturing services may rise. The market potential for OEM production is influenced by competition among OEM providers. Price, quality, dependability, manufacturing capacity, and ability to meet specific customer requirements all have a substantial impact on market share and potential.
Contents of Project Report
A project report helps you identify whether a project is worth pursuing. It presents the holistic view and brings complete insight of the business and its activity.
It acts as a guide for all the business operations, aids in taking all financial decisions related to the existing businesses and to the start-ups. It serves as roadmap to the business and provides information to the outsider who are wanting to know more about the business.
You will have the opportunity to build new goals and expansion ideas in one single document. Everyone, from the banks to potential investors, will need to have a look at the project report before they shell out any money.
A well drafted project report generally consists details about:
- Brief History of the Business
- The Promoters
- SWOT Analysis
- Industry Outlook
- Past Financial Statements
- Projected Financial Statements
- Infrastructure and Human Resource required
- CMA data
- Business model
- Requirement of Working Capital Funds
- Means of Finance
Other relevant information, if any.