Feasibility Report On Lithium Ion Battery Manufacturers
Lithium-ion battery manufacturers are companies that produce rechargeable batteries using lithium-ion technology. These batteries are essential for powering devices like smartphones, laptops, electric vehicles, and renewable energy storage systems due to their high energy density and eco-friendly characteristics.
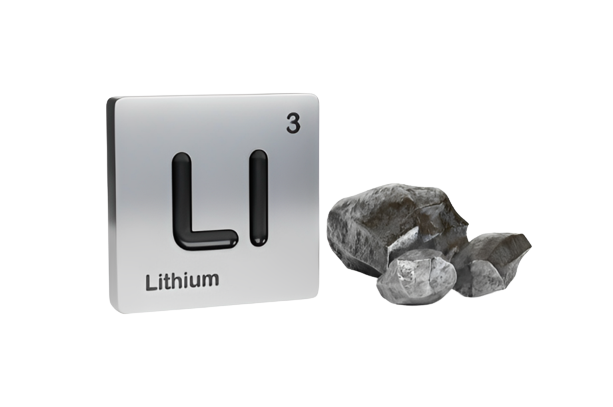
Introduction
Feasibility Report For Lithium Ion Battery Manufacturers.
Lithium-ion is the most extensively used rechargeable battery chemistry today. Lithium-ion batteries power daily devices such as cell phones and electric vehicles. A lithium-ion battery is made up of one or more lithium-ion cells and a protective circuit board. When the cell or cells are installed inside a device with a protective circuit board, they are referred to as batteries.
The lithium-ion battery cell is made in three stages: electrode fabrication, cell assembly, and cell finishing. Each of these stages includes sub-processes that range from coating the anode and cathode to assembling the various components and finally packing and testing the battery cells. The most common forms of cells are Prismatic, cylindrical, and pouch, and while the cell design varies, the production procedures are quite similar. Manufacturing accounts for around 25% of the cost of the Li-ion battery.
A lithium-ion battery’s main components are a positive electrode (cathode), a negative electrode (anode), and an electrolyte. A lithium metal oxide cathode, such as lithium cobalt oxide (LiCoO2), lithium nickel manganese cobalt oxide (NMC), or lithium iron phosphate (LiFePO4), is frequently used. The anode is usually graphite, while the electrolyte is often a lithium salt mixed in an organic solvent.
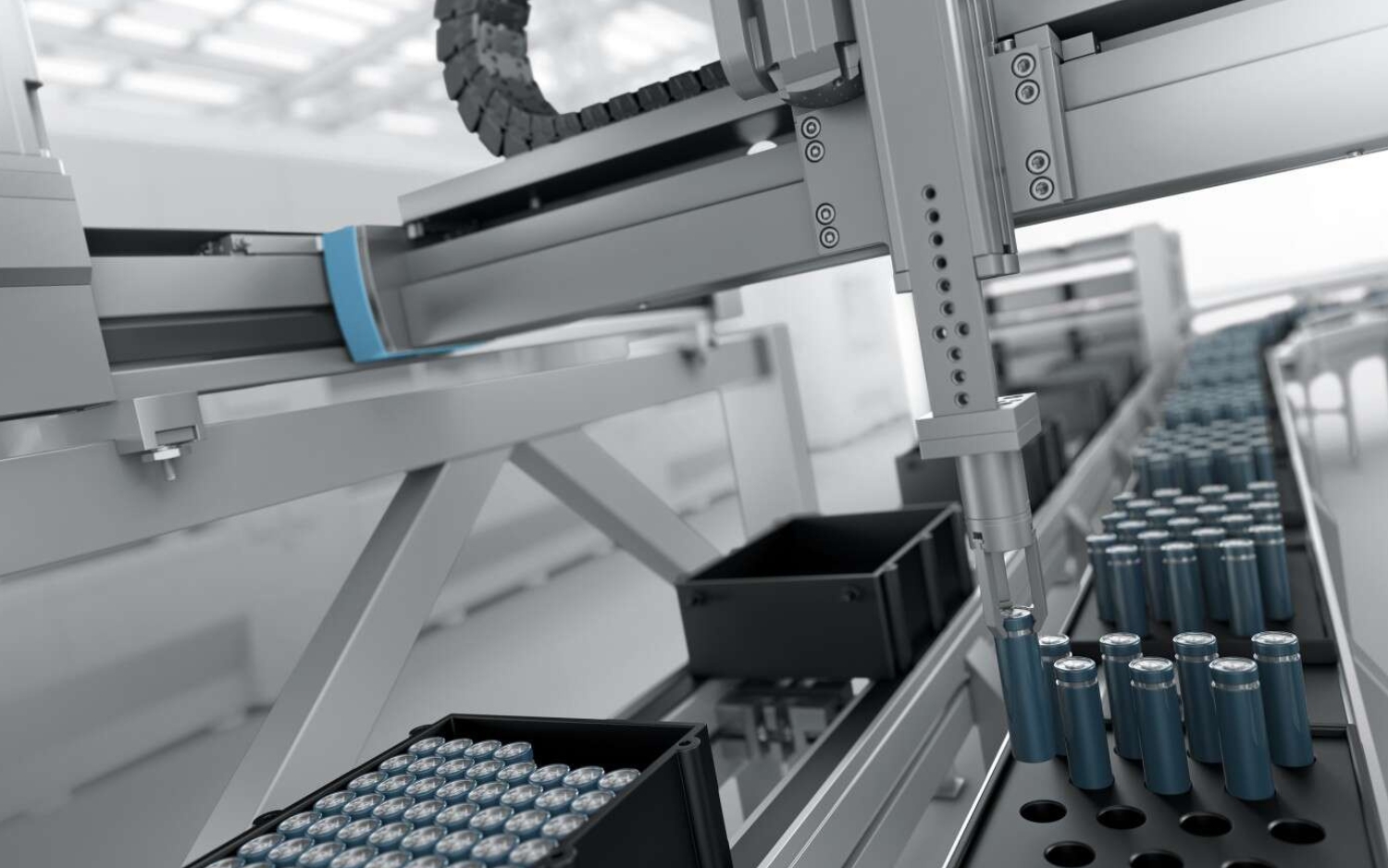
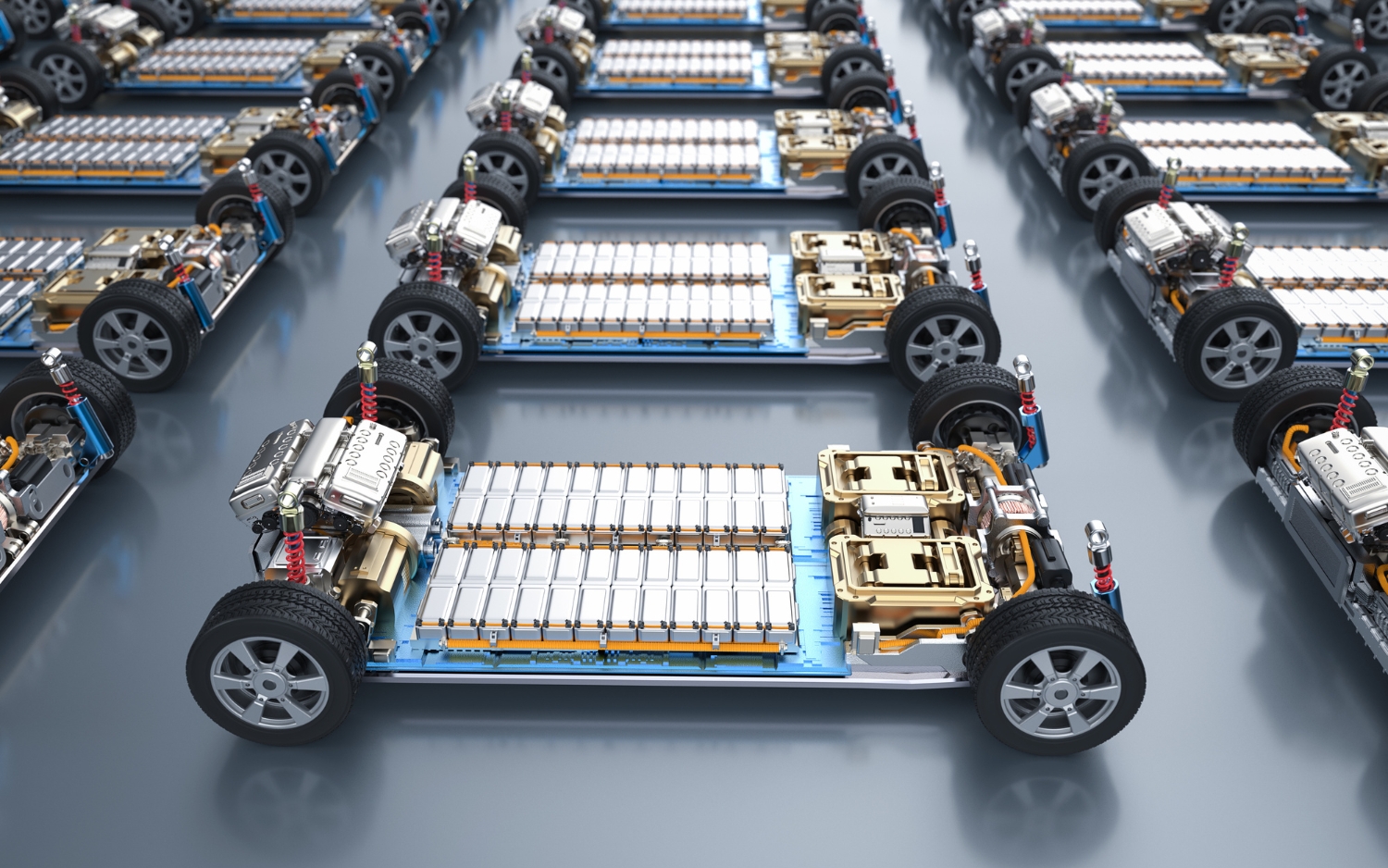
Electrode materials and conductive binders are mixed with a solvent to create a uniform slurry. Anode material, typically carbon, and cathode, a lithium metal oxide, are processed separately to prevent contamination. The slurry is then applied to both sides of current collectors (aluminum foil for cathode, copper foil for anode) using various tools. Coating thickness is controlled during this process. The coated foil is dried in an oven to remove the solvent. Calendaring follows, compressing the coated foils to adjust their physical properties. After cleaning, the electrodes are cut into narrow strips and recoiled. Residual moisture and solvent are removed in a vacuum oven. Purchased components include active materials, additives, solvents, binders, aluminum foil, and copper foil.
Charging and discharging cycles are used to produce a protective layer between the electrolyte and electrode during the battery cell development process. The gas created during the initial charge is evacuated, and the cell is vacuum-sealed. Ageing occurs after cell creation, and it monitors cell properties and performance. High and low-temperature ageing is performed, and if no major changes occur, the cell is considered functioning. The cells are next subjected to an end-of-line test, which includes capacity measurements, pulse testing, resistance measurements, inspections, and leakage tests. Cells are combined into battery packs after successful testing. The process of formation and ageing accounts for 32% of the whole manufacturing process.
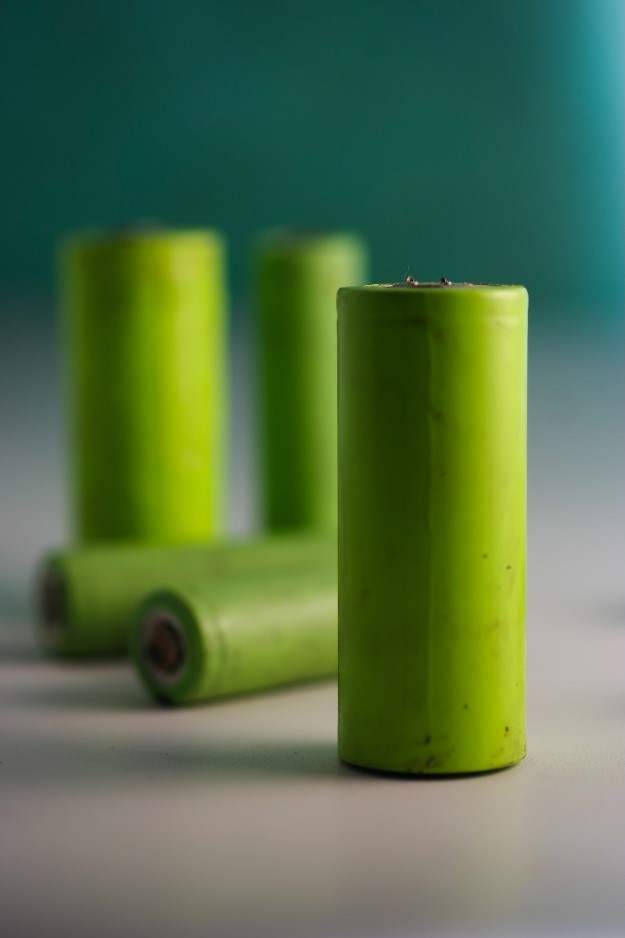
Feasibility Report Sample On Lithium Ion Battery Manufacturers
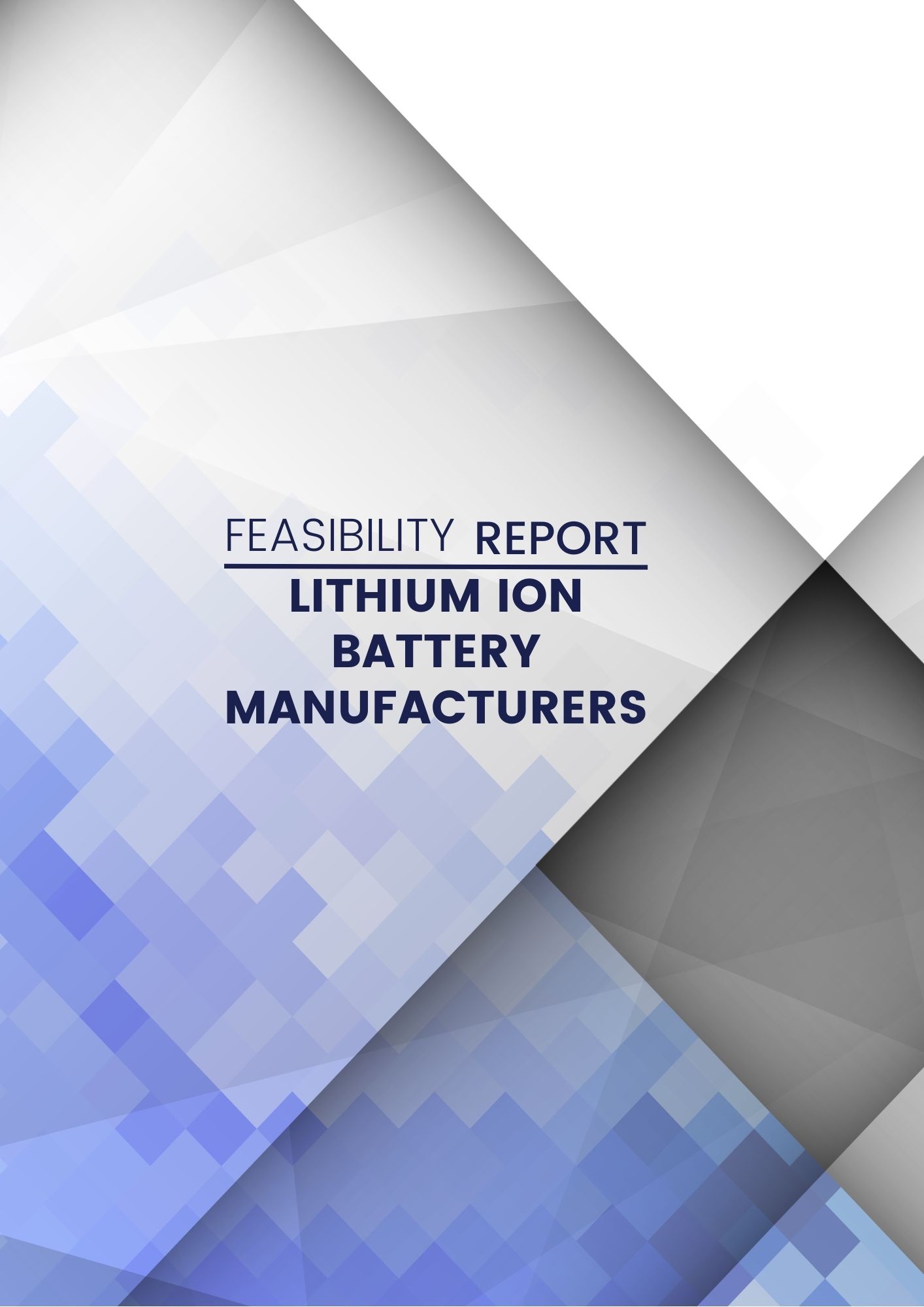
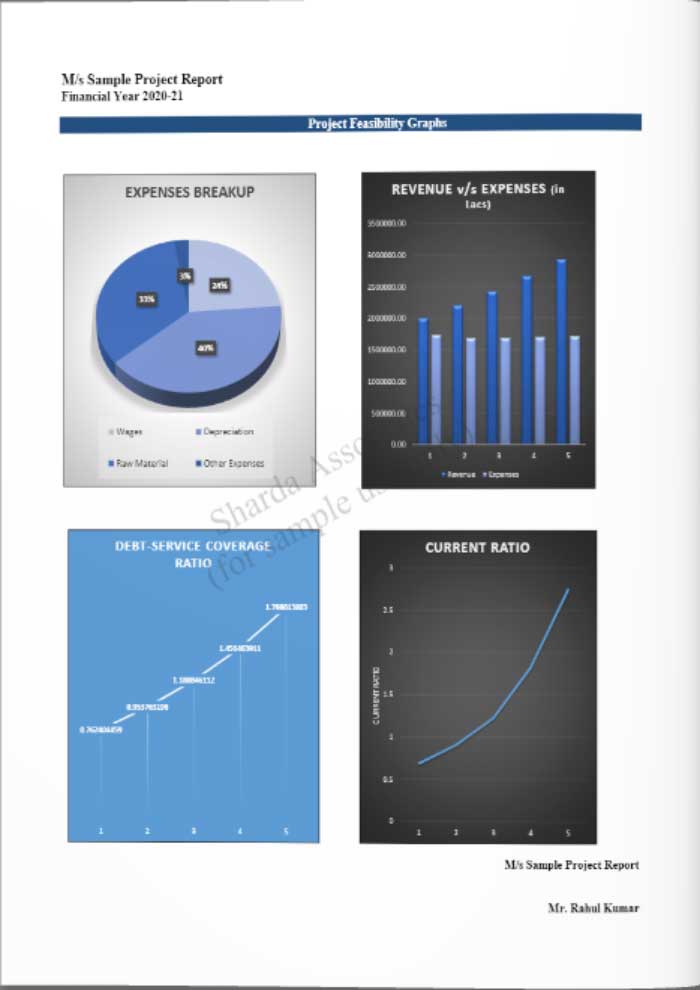
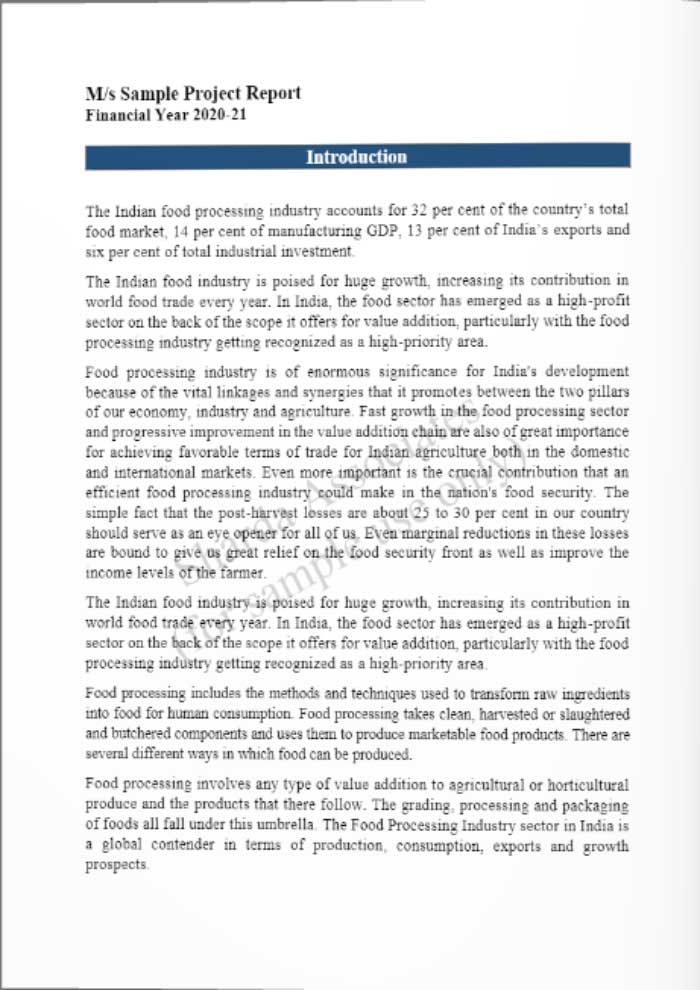
Market Strategy on Lithium Ion Battery Manufacturers
The India Lithium-ion Battery Market is predicted to be worth USD 2.48 billion in 2023, rising to USD 5.49 billion by 2028, at a CAGR of 17.21% during the forecast period (2023-2028).
The market is divided into applications such as automotive, consumer electronics, energy storage systems, industrial, and others. The automotive industry is likely to be the most dominant use for lithium-ion batteries. Rising public knowledge of the benefits of battery-powered vehicles, as well as rising petrol and diesel prices, have drawn consumers to these electric or hybrid vehicles, particularly in Asia Pacific, North America, and Europe. The consumer electronics industry is thought to be the most rapidly developing use for lithium-ion batteries. The continued advancement of the consumer electronics industry has resulted in an increase in the use of lithium ion batteries in various applications. They provide numerous benefits such as greater power capacity, less pollution, and increased safety.
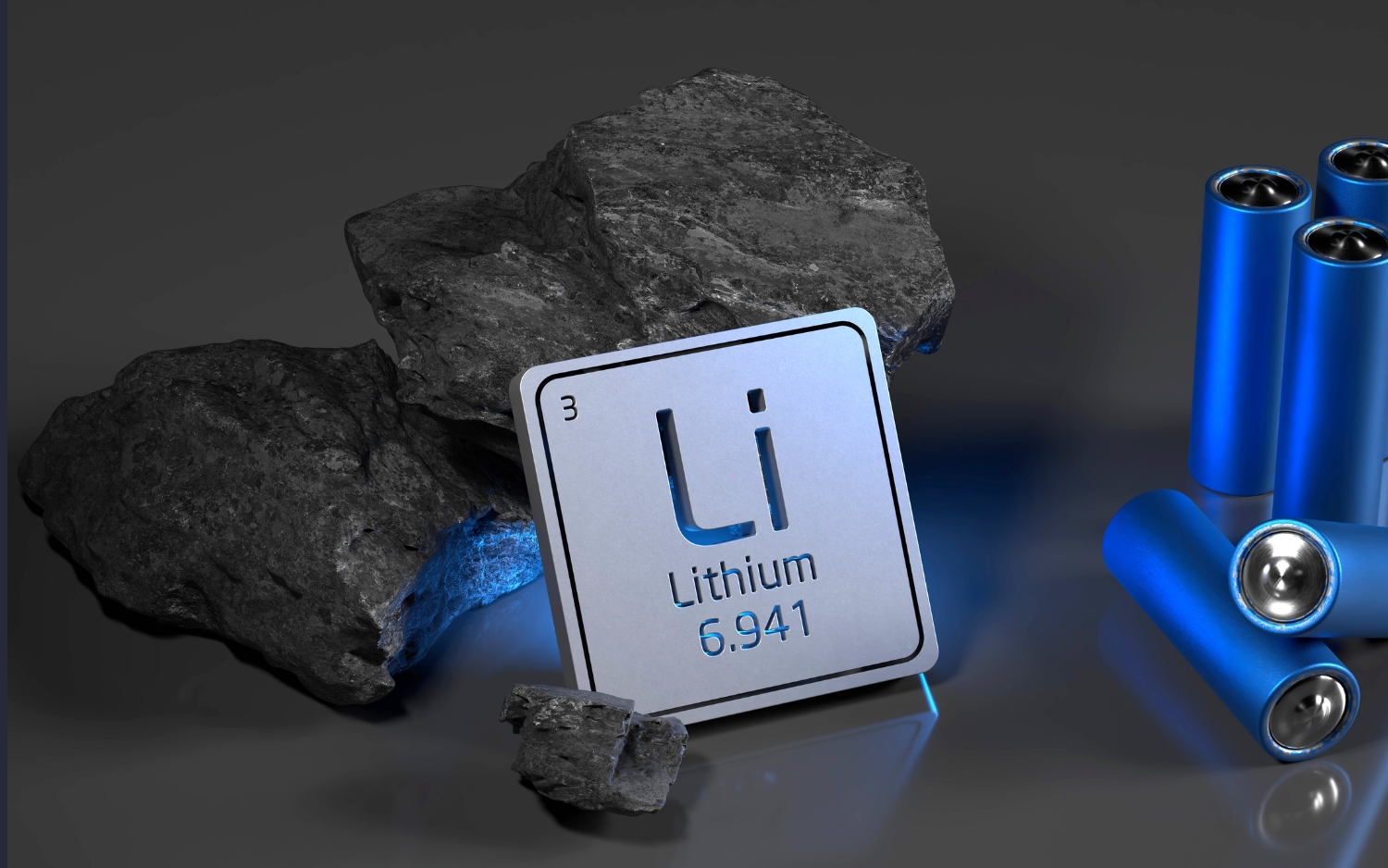
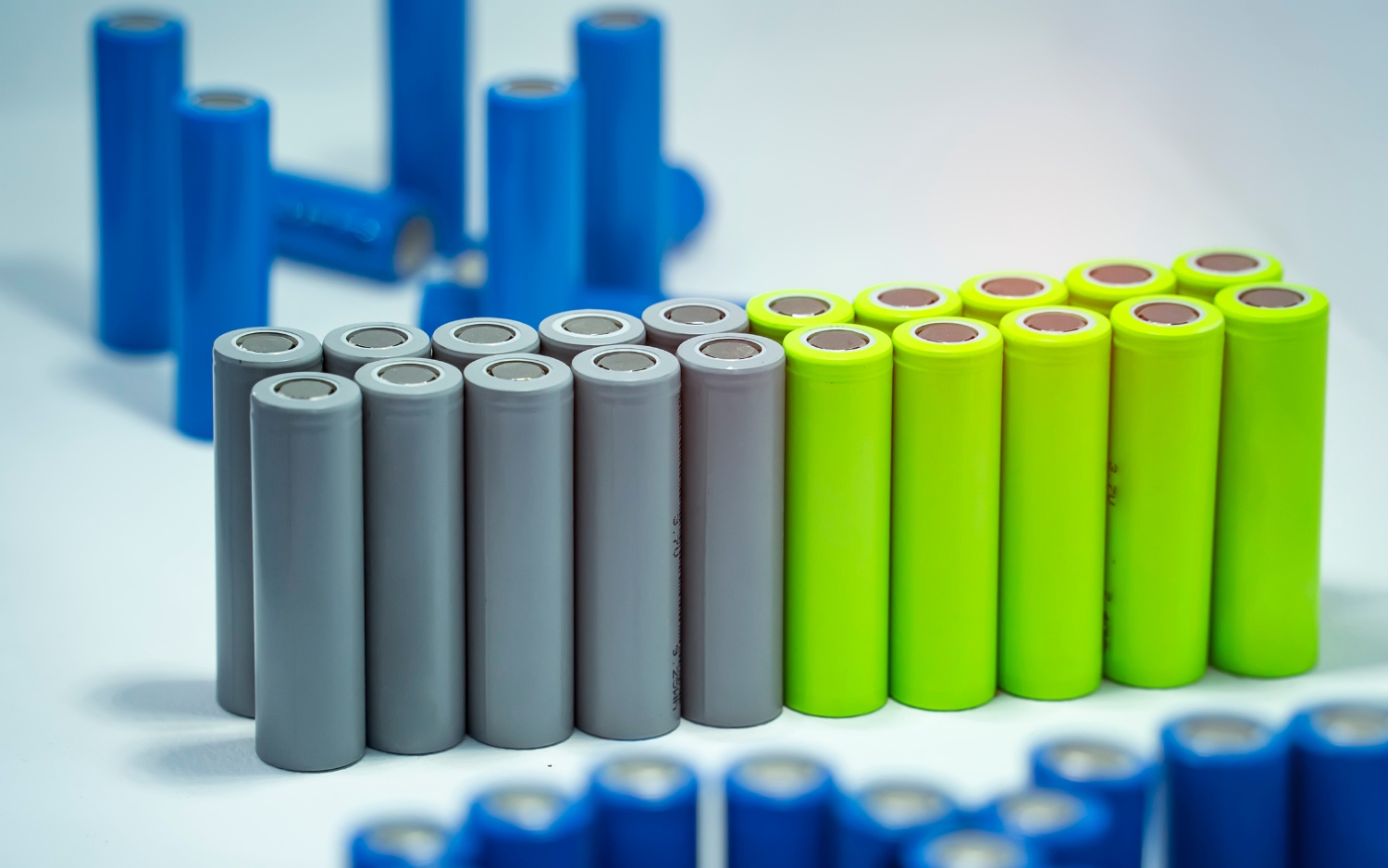
However, challenges such as an uneven supply chain network, a mismatch between supply and demand, local protectionism, and quality differences are impeding market revenue growth. These inefficiencies could exacerbate battery supply issues for industries such as new vehicles and solar power storage installations, reducing industry revenue development. Furthermore, lithium-ion batteries and cells are not as long-lasting as other rechargeable technologies, necessitating protections against overcharging and reckless disposal. Furthermore, the current in these battery types must be controlled at safe levels at all times.
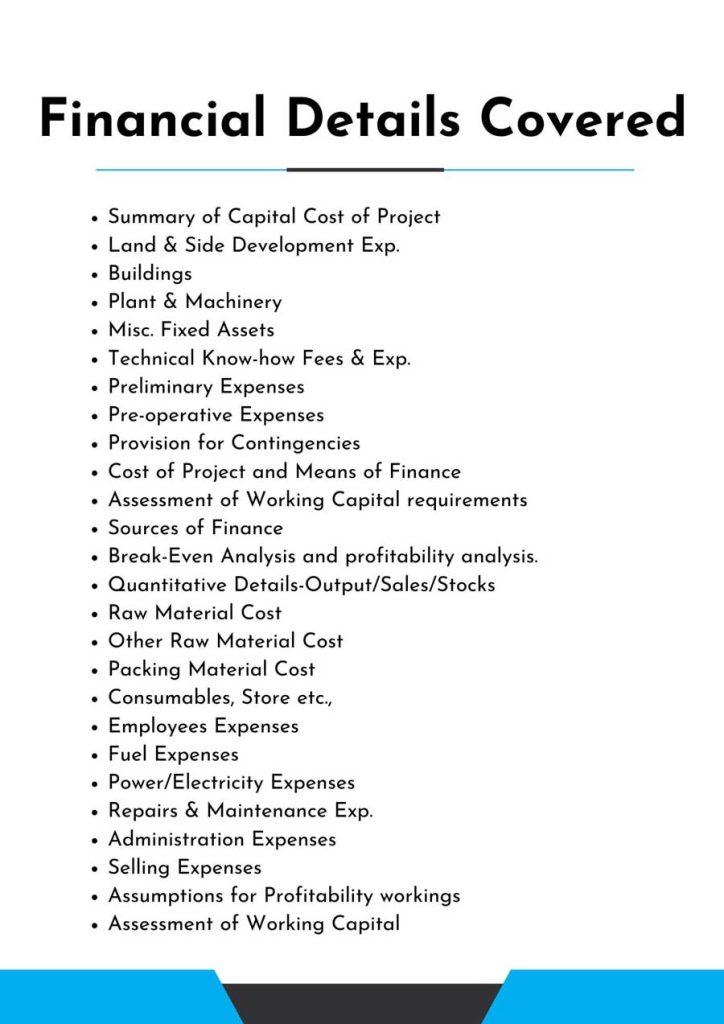

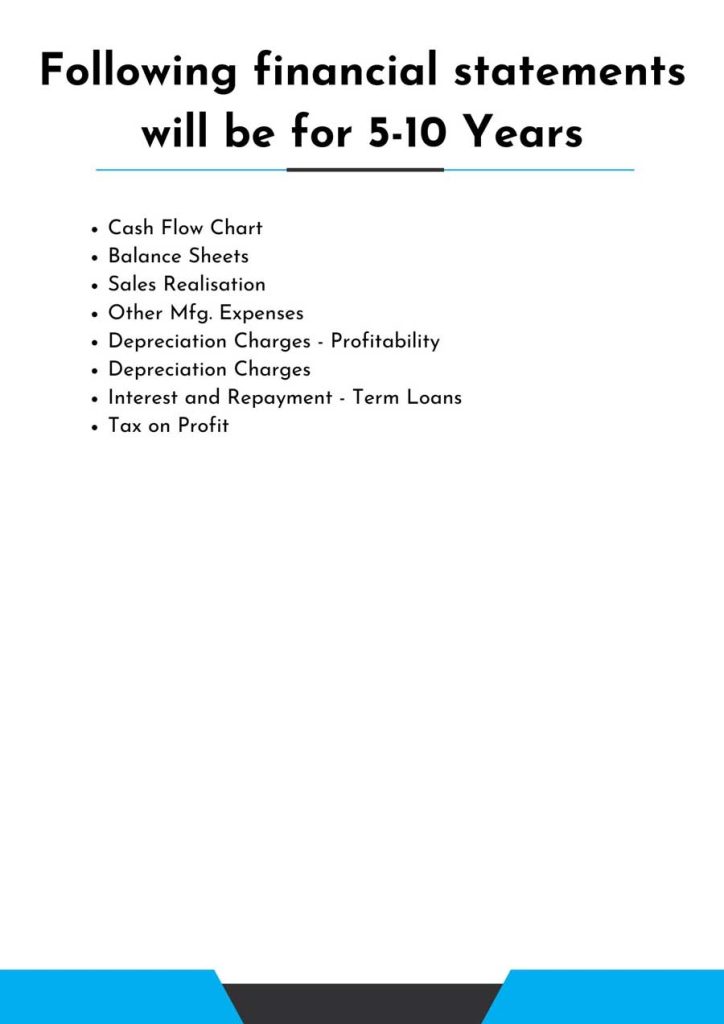