Project Report For Aluminium Ingot Manufacturing
Introduction
Project report for Aluminium Ingot Manufacturing is as follows.
Aluminium ingots are non-ferrous metal ingots made by pouring molten aluminium into moulds. These moulds are available in a number of sizes and forms, and the ingots produced by them have a variety of appearances.
The ingots are either shipped to other processors or flattened into thin sheets and utilised to produce new cans.
Aluminium ingots are used in a variety of industries, including automobile, home appliances, construction, mechanical, and consumer products.
Project Report Sample On
Aluminium Ingot Manufacturing
Get Completely Custom Bankable Project Report
While UBCs (Used Beverage Cans) are the most obvious component of the aluminium scrap recycling narrative, they are far from it. In reality, UBC recycling accounts for less than 30% of the total tonnage of recovered aluminium consumer items.
The expansion of the market for recycled aluminium scrap is mostly attributable to economic factors. Today, “Aluminum Recycling” is less expensive, quicker, and more energy-efficient than ever before, and it achieves a greater aluminium recovery rate than ever before.
Furthermore, as compared to primary aluminium, recycled aluminium only takes roughly 10% of the capital equipment to produce the same amount of ingot.
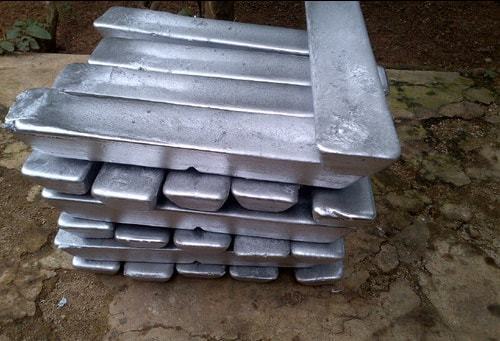
However, changing raw material costs are a key stumbling block to the worldwide aluminium ingots market’s expansion. Furthermore, the availability of diverse alternatives is another issue that may impede worldwide market development to some level.
Key companies’ increased focus on developing innovative products to stay ahead of the competition and stay in the market, as well as their focus on entering the untapped market, are expected to create potential opportunities for global market players in terms of business expansion and revenue growth.
Furthermore, growing strategic actions like mergers and acquisitions, joint ventures, and capital expenditures by investors are projected to promote target market development in the future years.
Market Potential Of Aluminium Ingot Manufacturing
Expenses
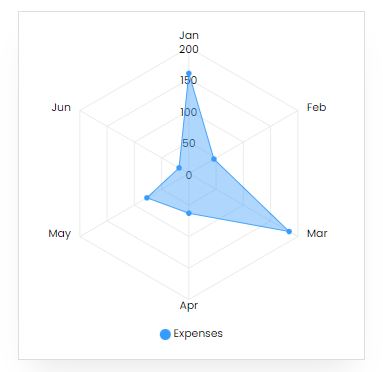
Product Cost Breakup
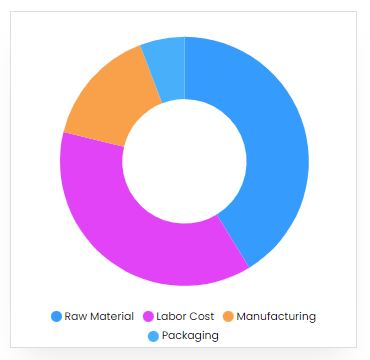
Reveneue Vs Expenses
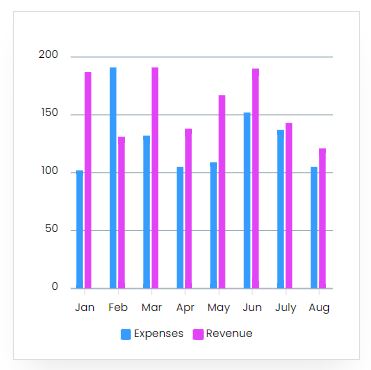
Market Trend
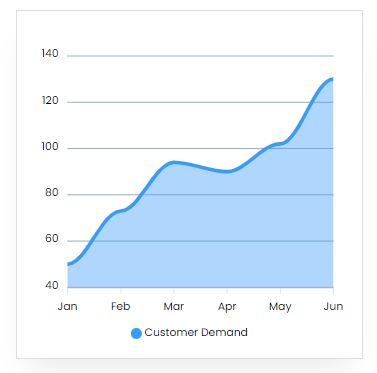
Aluminum is important in today’s industrial sector because of its inherent and diverse features such as strength-to-weight ratio, lightweight, corrosion resistance, nontoxicity, thermal and electrical conductivity, and so on.
Even after factoring in the expenses of collection, separation, and recycling, recycling aluminium waste delivers significant cost savings when compared to making new aluminium.
Aluminium is smelted to generate ingots, which are then processed further as needed. On a big scale, different grades of ingots are created according to the needed purity, which may subsequently be utilised to produce castings and specific electrical applications in the automobile sector. Ingots come in a variety of forms, sizes, and purity levels, with the maximum purity level being 99.7%. Ingots are raw materials that are moulded into the desired forms using a secondary shaping operation before being processed in end-use applications.
Cold and hot working, as well as milling and cutting, are all techniques that are required to create the final product.
Rapid industrialization in both developed and developing countries, as well as increased construction and reconstruction activities around the world, combined with the wide application of aluminium ingots in the construction sector for manufacturing windows, proofing doors, screens, and other products, are some of the key factors expected to continue to drive global market growth.
Other factors boosting the development of the global aluminium ingots market include increased emphasis on technical improvements in the packaging sector and increased acceptance of aluminium ingots in the manufacture of cans and aluminium foils due to its lightweight and easy moldability.