Project Report For Cement Rotary Klin Machine
Introduction
Project Report for Cement Rotary Klin Machine is as follows.
Cement rotary kilns are cement rotary calcining kilns (sometimes called rotary furnaces). The kiln body is a cylinder vessel with a slight inclination to the horizontal level. The raw ingredients are fed into the vessel from the higher end and moved to the lower end, where they are churned and mixed by the inclination and rotation of the kiln. The kiln burner generates a lot of heat by burning fuel. This type of heat is typically conveyed to materials by flame radiation, hot gas convection, kiln brick conduction, and so on, causing a chemical reaction between raw materials and eventually forming clinker.
Cement rotary kilns are used in cement plants to calcine cement clinker and are classified as dry cement kilns or wet cement kilns. In the metallurgical industry, metallurgical and chemical rotary kilns are primarily used. The lime rotary kiln is the primary piece of equipment used in iron and steel plants, ferroalloy plants, calcium carbide plants, and magnesium metal facilities for calcining active lime and light burnt dolomite.
A cylinder, a supporting device, a drive gear, a refractory lining, a catch-wheel device, a kiln head sealing device, and a kiln are the essential elements of a cement rotary kiln tail sealing device, a kiln hood, and other components. A big gear ring is fastened to the cylinder with a spring plate near the kiln tail, and some pinions below engage with it to form the drive gear. In normal operation, the primary drive motor transfers power to this gear device via the reducer to power the rotary kiln. The raw material normally enters the rotary kiln from the upper end and moves slowly to the other end as the chamber rotates.
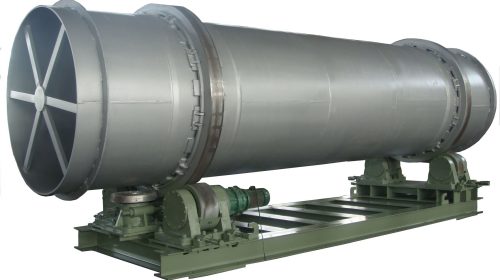
In the pyroprocessing stage of making Portland cement and other types of hydraulic cement, calcium carbonate combines with silica-bearing materials to create a combination of calcium silicates. Cement kilns are employed for this process. The cement kilns at the hub of this processโ whose capacity often determines the capacity of the cementโproduce more than a billion tonnes of cement annually plantโare the key to this process.
The main focus of cement manufacturing technology has been on increasing kiln efficiency because this is the stage of cement production that uses the most energy and emits the most greenhouse gases. Around 2.5% of all non-natural carbon emissions globally come from emissions from cement kilns, which is a significant source of greenhouse gas emissions.
In this process, raw materials are heated to high temperatures and subsequently breakdown and cause chemical reactions, causing their state to change. The heat source of indirect fired rotary kilns is normally supplied by the kiln burner located outside the kiln. While the heat source of the direct-fired rotary kiln is located inside the kiln, this method safeguards the integrity of raw materials.
Furthermore, the rotation speed and temperature of the cylinder are closely regulated and can be modified to suit various desired procedures and material applications. After the calcination is finished, the clinker will be pre-cooled in the chamber before being delivered to the cooler for further chilling.
Project Report Sample on
Cement Rotary Klin Machine
Get Completely Custom Bankable Project Report
Market Potential for Cement Rotary Klin Machine
The value of the worldwide rotary kiln market was approximately USD 583.40 million in 2021, and is projected to increase to nearly USD 684.52 million by 2028, which is with a CAGR of roughly 2.70 % over the forecast period.
To accommodate the increased demand for cement and steel in the building industry, cement and lime makers are establishing and developing new factories. These businesses are concentrating on growing production capacity by constructing new cement and lime facilities, which will drive demand for rotary kiln systems. Alternative fuels are gaining popularity on the market, including waste oil, solvents, textiles, waste paper, rice husks, sawdust, and sewage sludge. Furthermore, construction and demolition wastes including wood, worn carpets, and old asphalt shingles are frequently used as low-carbon alternative fuels. Utilizing alternative fuels conserves resources and reduces CO2 emissions.
The global rotary kiln market is classified by Technavio as part of the global industrial machinery market. The levels of growth in the rotary kiln market over the anticipated period will be determined by the external factors that have a significant impact on the parent marketโs potential for growth in the ensuing years that have been thoroughly examined in our research report.