Project Report For Clinker Manufacturing
Introduction
Project report for Clinker Manufacturing is as follows.
Clinker is the most widely used cement in the world, and it is manufactured at high temperatures that chemically mix the constituents to form new components such as calcium silicates and calcium aluminates.
Cement is formed when cement clinkers are crushed with roughly 5% gypsum. When mixed with water, these chemicals allow the cement to set and produce strong connections that can endure pressure, water immersion, and other factors.
Get Completely Custom Bankable Project Report
Clinker is a lump or nodule, generally 3-25 mm in diameter, created in the Portland cement manufacturing process by sintering limestone and alumino-silicate during the cement kiln stage.
Cement clinkers are created by heating cement ingredients in a kiln. Limestone, clay, bauxite, and iron ore sand are burnt in specified quantities in a rotating kiln at 2,770ยฐ Fahrenheit (1,400ยฐ Celsius) until cinder lumps, also known as cement clinkers, form.
Cement clinkers are typically processed with gypsum to generate the fine powder that is later combined with a liquid to produce cement, while some producers transport cement clinkers in lump form to reduce dust. Cement is significantly used in the production of mortar, grouts, and concrete, and cement clinkers are the initial step, post-firing, in the production of cement.
Cement has strong bonding properties when coupled with gypsum and water to generate a hydration reaction, and it forms about one-tenth of concrete when mixed with rocks, sand, and other minerals and is utilised in building construction all over the world.
Concreteโs adaptability makes it an appropriatthe e material for a wide range of construction projects, from skyscrapers to pool sides. When concrete has outlived its usefulness, it can be recycled and transformed back into cement clinkers by proper processing.
Portland cement is made by grinding clinker (typically with the addition of a little gypsum, or calcium sulphate dehydrate). It can also be used with additional active components or chemical admixtures to make ground granulated blast furnace slag cement, pozzolana cement, and silica fume cement.
Market Potential Of Clinker Manufacturing
Expenses
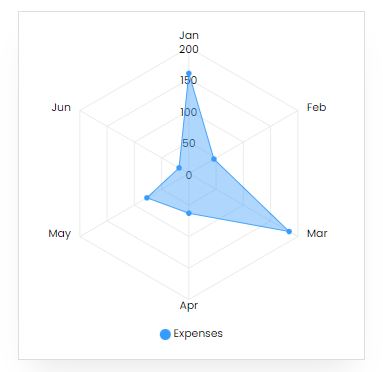
Product Cost Breakup
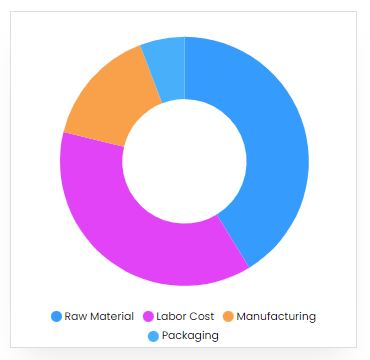
Reveneue Vs Expenses
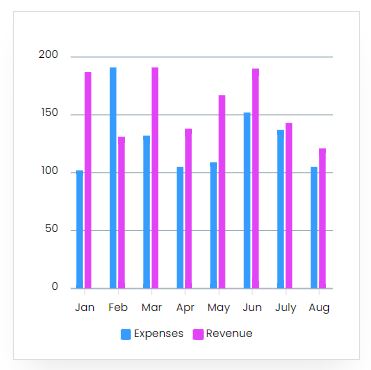
Market Trend
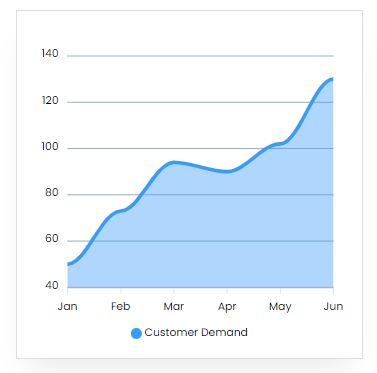
The cement sector has benefited greatly from the infrastructural development. The sector has a bright future because of strong demand and ample supply. The Indian cement industry is the second biggest after China, with a total capacity of 165 million tonnes. The cement business is dominated by 20 corporations that account for more than 70% of the market.
No single firm accounts for more than 12% of the market. Major players like as L&T and ACC have been quite successful in closing the demand-supply gap. The private housing industry consumes the most cement (53 percent), followed by the government infrastructure sector. Similarly, the northern and southern regions utilise roughly 20%-30% cement, whereas the middle and western regions consume just 18%-16%.
After China, India is the worldโs second largest cement production. From laying economic concrete blocks to waving flyovers, the cement industry has demonstrated and continues to demonstrate a bright future.
In India, domestic demand for cement is rapidly expanding. The cement sector has contributed around 8% to Indiaโs economic development. Outsiders (foreign players) are looking at India as a big market to engage in through mergers or FDI (Foreign Direct Investment).
The cement sector has a long way to go since the Indian economy is on the edge of expansion. The corporation continues to place a premium on cost-cutting measures such as increased productivity, lower energy costs, and lower logistical charges.
Because of the high correlation with GDP, the cement industry is likely to increase in tandem with the economy. Road and housing constructions would be future drivers of cement demand growth in India.
As per the Working Group report on Cement Industry for the formulation of the 11th Plan, cement demand is expected to grow at a rate of 11.5 percent per year during the 11th Plan, with cement production and capacity estimated to be 269 million tones and 298 million tones, respectively, by the end of the 11th Plan, with capacity utilisation of 90 percent.