Project Report For Foam Manufacturing
Introduction
The project report for Foam Manufacturing is as follows.
Foam has been used to put out fires inflammable and combustible liquids for many years. Unlike other extinguishing agents such as water, dry chemicals, CO2, and so on, a stable aqueous foam may extinguish a flammable or combustible liquid fire by chilling, removing the flame/ignition source from the product surface, suppressing vapours, and smothering.
It can also protect against reflash or reignition for long periods of time. Water, when poured directly to the surface of a conventional hydrocarbon fuel, is heavier than most of those liquids and will sink to the bottom, having little or no influence on extinguishment or vapour suppression. If the liquid fuel gets up to 212 degrees Fahrenheit, the water beneath the fuel surface may boil, releasing the fuel from the controlled region and spreading the fire.
Project Report Sample Of
Foam Manufacturing
Get Completely Custom Bankable Project Report
As a result, foam is the principal fire-fighting material for any possible risks or regions where flammable liquids are carried, processed, stored, or used as a source of energy. Firefighting foam is nothing more than a stable mass of tiny air-filled bubbles with a lower density than oil, gasoline, or water. Water, foam concentration, and air are the three constituents that makeup foam. These three materials combine to make a homogenous foam blanket when combined in the proper quantities.
The two types of foam materials that are most frequently used are closed cell foam and open cell foam. Both kinds of foam materials perform better than average at protecting and cushioning. Comparing foam to other hard plastic and wood components, comfort and protection are its greatest advantages. EVA foam, polyethylene foam, polyurethane foam, and foam rubber materials are a few of the most popular varieties.
The result of introducing gas bubbles into a polymer is foam. It is a permeating, lightweight material that is available in many different varieties. Simply said, expanded plastic and rubber are versions of foam material. Because of their typical resilience and great elasticity, foam is perfect for providing strong cushioning and supporting for other products.
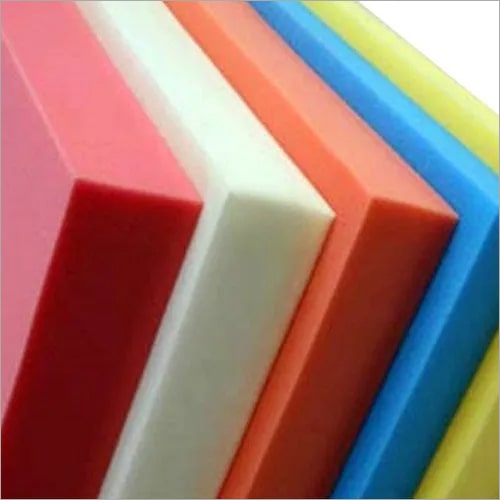
Foam makers are always trying for sustainability in their business methods, in light of rising concerns about the use of fossil fuels and the impact of plastics on the environment. Oil price volatility has had a substantial influence on the foam industryโs profitability in recent years. As a result, bio-based polyols that may be utilised to make foam were developed.
Theyโre also less susceptible to hydrolysis and more thermally stable. Urethane Soy Systems, Bio-Based Technologies, Dow Chemical Company, Cargill, Inc., and MCPU Polymer Engineering are among the leading makers of soy-based polyols.
Market Potential Of Foam Manufacturing
The foam market is expected to grow at a CAGR of 4.8 percent between 2021 and 2026, from USD 93.9 billion in 2021 to USD 118.9 billion in 2026. The rise of numerous end-use industries is propelling the market forward. In China, India, and Brazil, increased investments in infrastructure, new housing developments, and non-residential building renovations have bolstered market growth.
Expenses
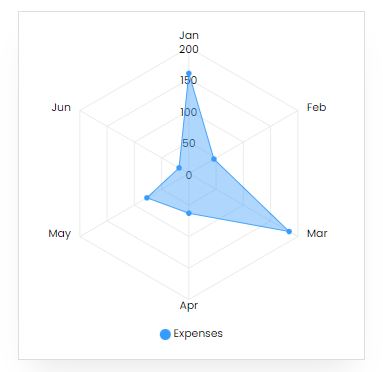
Product Cost Breakup
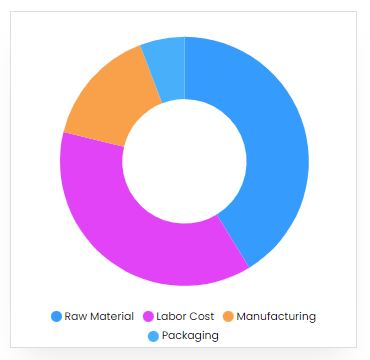
Reveneue Vs Expenses
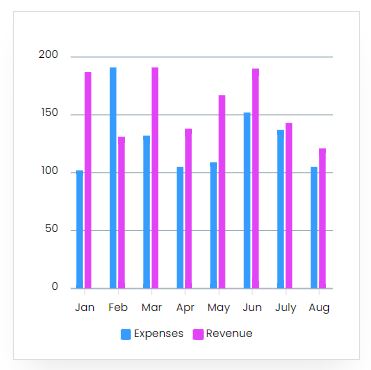
Market Trend
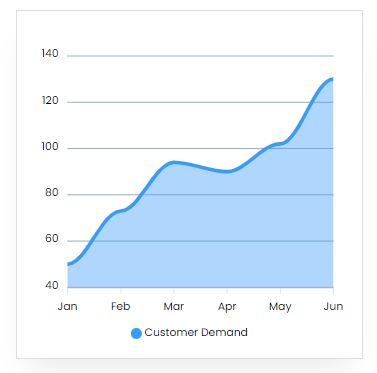
In the construction business, foam is used for forging, pipe-in-pipe, doors, roof boards, and slabs. In both residential and commercial buildings, PU foam is commonly utilised for interior wall and roof insulation. Crafts and architectural model construction also use extruded polystyrene material. Because it is light but stiff, with strong thermal insulation and great impact resistance, EPS is an ideal material for building and construction.
Packaging is required for the protection and insulation of all types of commodities, particularly in the food sector and the online shopping (shippable materials) industry. The usage of foam in packing is rising as people become more mindful of the safety, quality, and upkeep of a productโs physical features.
The cost structure of goods is determined by the price and availability of raw materials. Benzene, toluene, polyol, and phosgene are the main basic components used to produce foam. These are petroleum-based derivatives that are susceptible to price swings. Due to increased global demand, unrest, and foreign military action in the Middle East, oil prices were very volatile in 2018-2019.
The foam industry has been impacted by price fluctuations in petrochemical-based raw materials during the last few years. Supply has been constricted and raw material prices have risen due to persistent global demand and capacity constraints in basic chemicals and resins.