Project Report For Grey Iron Castings
Introduction
Project report for grey iron castings is as follows.
Grey iron casting refers to cast iron with a graphitic microstructure. Its name refers to the grey microstructure it produces, which is made up of loose graphite particles. Gray iron is a common technical alloy due to its low cost and good machinability (due to the graphite lubricating the cut and dispersing the chips). Because graphite flakes self-lubricate, they are resistant to galling and wear. Gray iron has excellent dampening capabilities due to graphiteโs ability to absorb energy and convert it to heat. It is the most common and widely used cast iron.
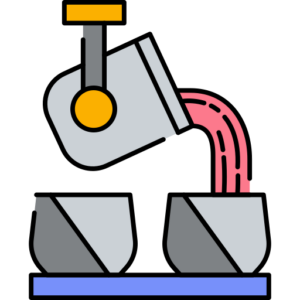
Product & Application of Grey Iron castings
The characteristics of cast iron are altered by the addition of various alloying elements. Because it aids in the formation of free graphite, silicon is the most significant alloy element.
A low silicon content permits carbon to remain in solution, creating iron carbide and producing white cast iron. A high silicon content drives carbon out of solution, resulting in graphite and the formation of grey cast iron. Other alloying agents include manganese, chromium, molybdenum, titanium, and vanadium, which counteract silicon by promoting carbon retention and the development of carbides in the microstructure, boosting tensile strength, impact strength, wear and heat resistance, corrosion resistance, and so on. Nickel and copper improve strength and machinability while having little effect on the amount of graphite produced.
It possesses a variety of attractive qualities that no other metal possesses while remaining one of the least expensive ferrous materials available to the engineer. Gray iron castings are widely available in almost all industrial domains and can be made in foundries with relatively small investments.
It is employed in machinery bodies and rotating machine housings where stiffness is more critical than tensile strength. Alloy grey iron is widely used in cylinder blocks for internal combustion engines, pump housings, valve bodies, machine tools, heavy earth movers, and stationary machinery. Due to its characteristics, it is also suited for electrical boxes and decorative castings. Grey cast iron is frequently used to create cast iron cookware and disc brake rotors due to its strong thermal conductivity and specific heat capacity.
Project Report Sample On Grey
Iron Castings
Get Completely Custom Bankable Project Report
The main raw resources are pig iron, cast iron scrap, and metallurgical coke. As additional alloying additives, minerals like molasses graphite, silicon, manganese, and moulding adhesives are employed.
Market Potential Of Grey Iron Castings
The size of the world market for iron casting, estimated at USD 101.17 billion in 2021, is anticipated to rise at a 6.1% compound annual growth rate (CAGR) from 2022 to 2030.
Expenses
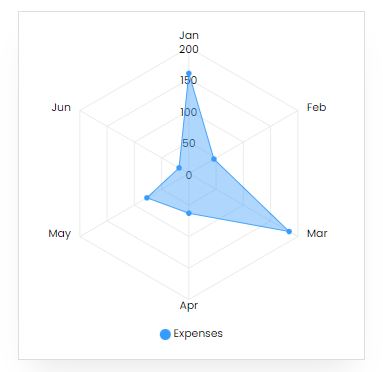
Product Cost Breakup
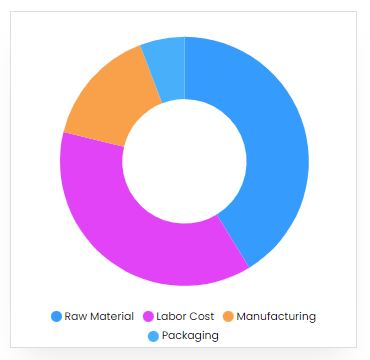
Reveneue Vs Expenses
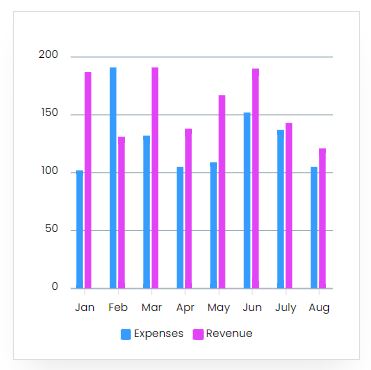
Market Trend
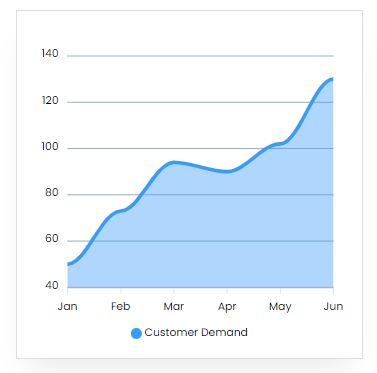
Grey iron casting accounted for more than 80 lakh MT of the more than 120 lakh MT produced by the Indian foundry sector in recent years. The foundry industry has exported goods worth more than $25 million. Casting production in India increased by 22%, compared to a 13.7% rise globally. Indian foundries account for about 10% of the global market.
Capital goods, the main end-user sector, are anticipated to grow from USD 35 billion to USD 115 billion by 2025, while the auto industry is anticipated to grow by 3.5 to 4 times from its current value of USD 74 billion to USD 260 billion to 300 billion. Even if these predicted plans only materialize to 75% of their potential, the Indian Foundry Industry will profit.
The need for premium grade โGrey Iron Castingsโ is rising from domestic products and components such as the auto industry, industrial machines, industrial valves, valve actuators, pumps, turbines, etc. The foundry market in India and for exports will develop steadily with a CAGR of over 10% by 2020.