Project Report For Hot Dip Galvanizing Plant
Introduction
Project Report For Hot Dip Galvanizing Plant is as follows.
A hot dip galvanising factory is a facility dedicated to the hot dip galvanization process, which is a popular way for preserving steel and iron against corrosion. The facility is made up of several pieces of equipment and procedures that allow a protective zinc coating to be applied to the metal surface, assuring its resilience and lifespan. The preparation of the metal surface is the first step in the procedure. The steel or iron products are completely cleaned to eliminate any dirt, grease, or rust from the surface. Typically, this is accomplished by a succession of chemical cleaning baths and mechanical treatments such as pickling and rinsing. The surface is ready for the following stage after it is clean and free of contaminants.
The cleaned objects are then submerged in a bath of molten zinc at a high temperature, often about 450°C (840°F). The bath includes a specialised flux that aids in the adherence of the zinc coating to the metal. To guarantee homogeneous coating, the products are carefully dropped into the bath with overhead cranes or other handling equipment. A metallurgical reaction happens between the iron or steel and the molten zinc when the items are immersed in the zinc bath. This reaction leads in the creation of a succession of zinc-iron alloy layers on the metal’s surface, giving good corrosion resistance. The thickness of the zinc coating may be adjusted by altering the immersion duration and bath temperature.
After the pieces have been soaked for the required time, they are carefully removed from the water, allowing excess zinc to drain. Any surplus zinc is eliminated using specialised draining or centrifuging equipment. The objects are next cooled, either by air or water quenching, to harden the zinc coating and finish the galvanising process. A hot dip galvanising plant would normally incorporate a number of auxiliary systems to aid in the galvanising process. These may include fume extraction systems to remove and treat any zinc fumes created during the process, wastewater treatment systems to manage the wastewater produced, and drying and curing ovens for drying and post-treatment of the galvanised products.
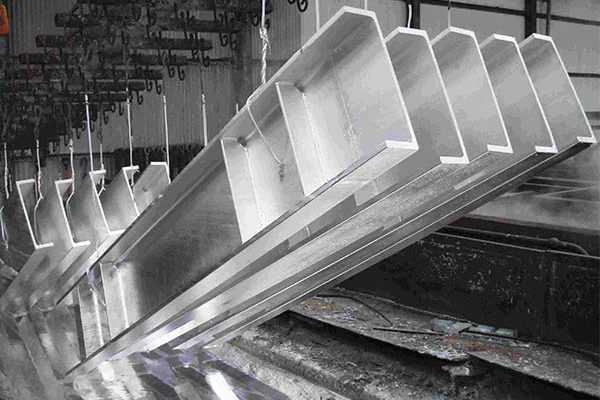
Types Of Hot Dip Galvanizing Plant
Batch Hot Dip Galvanising Plant: This is the most frequent and conventional type of plant. It is made up of a succession of galvanising baths and overhead cranes for immersing and removing individual objects. Batch machines are ideal for lower production quantities and provide flexibility in processing objects of varied sizes and forms.
Continuous Hot Dip Galvanising Plant: This plant is designed for high-volume manufacturing and continuous processing of long and narrow items like steel coils or strips. Following a succession of pre-treatment tanks, the articles are fed through a continuous galvanising furnace and cooling section. Continuous plants are extremely efficient and productive.
Centrifuge Hot Dip Galvanising Facility: This facility removes surplus zinc from galvanised objects using centrifugal force. Following immersion in the zinc bath, the objects are quickly spun in a centrifuge to remove the surplus molten zinc. This equipment is typically utilised for tiny goods or fragile objects that require precise coating thickness.
Modular Hot Dip Galvanising Plant: Modular plants are easy to build and relocate. They are made up of pre-fabricated modules that may be joined and dismantled according to manufacturing requirements. These plants are ideal for situations with limited space or that require temporary galvanising.
Market Potential Of Hot Dip Galvanizing Plant
The market for hot-dip galvanised steel products will reach an estimated value of USD 1.93 billion and expand at a CAGR of 42.5% from 2021 to 2028.
The increased ability of hot-dip galvanised steel to combat rust and corrosion has resulted in their widespread use in outdoor applications such as automotive, construction, general industries, and agriculture, among others, which is a key factor driving the growth of the hot-dip galvanised steel products market.
Increased renovation activities, as well as increased investment in residential and commercial projects, commercial and industrial construction in developing economies such as India and China, and increases in per capita income and spending, GDP growth, and urbanisation in several Asia Pacific economies such as Singapore, Malaysia, and Thailand, are among the major factors driving the hot-dip. Furthermore, increased research and development efforts in the industry, as well as an increase in demand from emerging nations, will provide new possibilities for the hot-dip galvanised steel products market during the forecast period of 2021-2028.
Project Report Sample On Hot Dip Galvanizing Plant
Need Help?
Create 100% Bankable Project Report