Project Report For Plastic Parts For Engineering Equipment
Introduction
Project report for plastic parts for engineering equipment is as follows.
Plastic parts have recently begun to replace metal elements in the engineering business. Converting from metal to plastic allows manufacturers to improve their products, save money, and simplify the manufacturing process. The purpose of transitioning from metal to plastic is to keep the product or componentโs integrity while decreasing cost and weight.
The development of tailored plastic resins that rival metal in terms of strength and endurance is critical to success. These plastic materials can provide improved wear surfaces while also having lower friction. Metal bearings, for example, can be avoided by embedding bearing components directly into the plastic part.
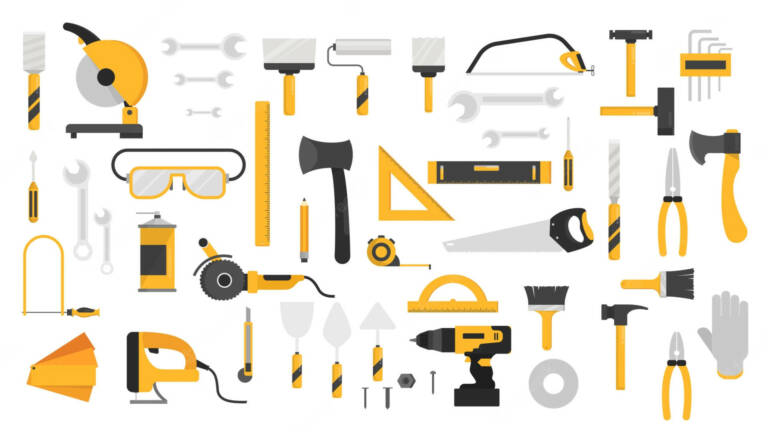
Plastic parts can be moulded into complicated shapes at a much lower cost than machining metal parts, and plastic parts are frequently superior when it comes to high-impact strength, fatigue life, or recoverable deformation. Conversions from metal to plastic frequently lead to increased performance and product value in addition to lighter parts, more uniform dimensions, and lower costs.https://shardaassociates.in/pr-samples/metal-casting/
Project Report Sample On Plastic Parts For Engineering Equipment
Get Completely Custom Bankable Project Report
The main kind of plastic required as a raw material for the project is PP, or polypropylene. Additional raw materials, such as plasticizer, colourants, binders, and packing materials, will be required. The Indian market has access to the majority of raw commodities.
Market Potential of Plastic Parts For Engineering Equipment
The market for engineering equipment is anticipated to increase from USD 141.99 billion in 2021 to USD 222.14 billion in 2028, with a 6.6% CAGR throughout that time.
Expenses
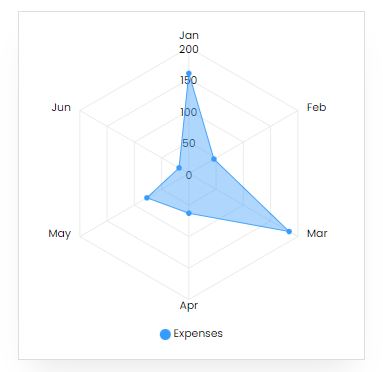
Product Cost Breakup
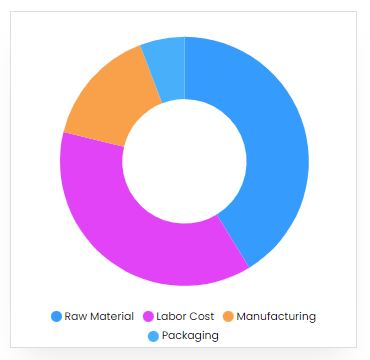
Reveneue Vs Expenses
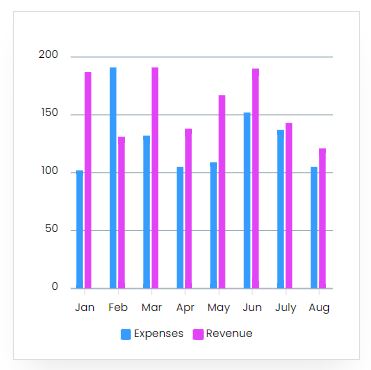
Market Trend
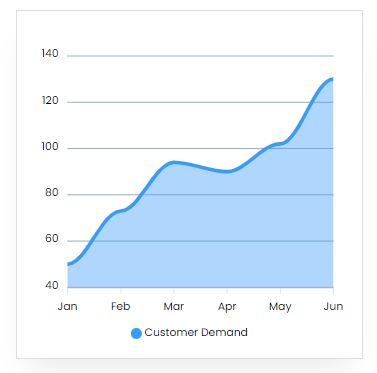
The manufacturing method of plastic injection moulding is used to create items from thermoplastic and thermosetting plastic materials. Material is forced into a mould cavity after being pressed into a hot barrel, mixed, and allowed to cool and harden to the mould cavityโs specifications.
A mould maker (or toolmaker) often creates metal moulds from metal, typically either steel or aluminium, and precision-machines them to form the features of the desired part after an industrial designer or engineer has designed the product.
Injection moulding is frequently used in the production of a wide variety of parts, from the smallest component to whole vehicle body panels. It is also used to make a large number of other objects, including wire spools, packaging, bottle caps, car dashboards, pocket combs, and the bulk of other plastic products available today.
The most popular method for producing parts is injection moulding. It is ideal for producing numerous units of the same thing. The advantages of injection moulding include high production rates, repeatable high tolerances, the use of a range of materials, low labour costs, little scrap waste, and a lack of post-mold finishing requirements. The Indian automobile industry is predicted to grow in another ten years.