Project Report For Plastic Injection Moulding
Introduction
Project report for Plastic Injection Moulding is as follows.
The method of plastic injection moulding involves melting plastic pellets (thermosetting/thermoplastic polymers) that, once flexible enough, are injected at pressure into a mould cavity, filling it and solidifying it to create the finished product.
At Protolabs, the thermoplastic injection moulding procedure is a regular procedure utilising an aluminium mould. Because aluminium conducts heat far more effectively than steel and does not require cooling channels, we can use the time we save on cooling to monitor fill pressure, address aesthetic issues, and create high-quality parts.
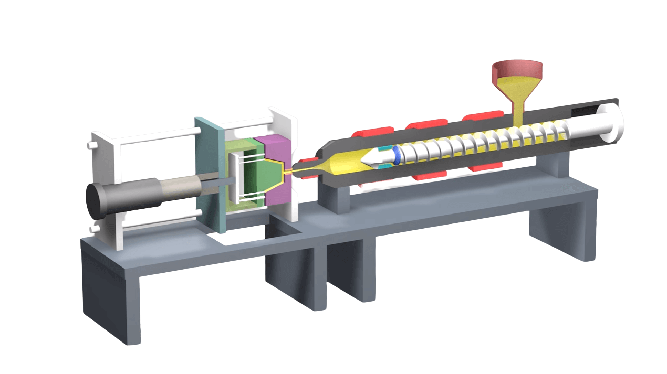
In a barrel, resin pellets are loaded before being melted, squeezed, and fed into the mouldโs runner system. The item is moulded after hot resin is shot through the gates into the mould chamber. The part is easily removed from the mould and dropped into a loading bin thanks to ejector pins. Parts (or the initial sample run) are packed and dispatched soon after the run is finished. Request your Free Design Cube, which features thick and thin finishes and surface treatments.
The polypropylene (PP) segment had the highest revenue share of more than 34% in 2021 as a result of rising PP use in packaging, home goods, and automotive components. Over the projected period, it is anticipated that increasing PP-based product penetration in protective caps, electrical connections & battery housings, and food packaging would further fuel its demand.
Due to their ability to resist corrosion and provide electrical insulation, polypropylene components are frequently found in electrical contacts and food packaging. The sector is anticipated to develop at the quickest rate during the forecast period due to the aforementioned causes.
Project Report Sample On Plastic
Injection Moulding
Get Completely Custom Bankable Project Report
In 2021, the packaging category contributed more than 30% of the total revenue share. To meet regulatory standards and end-user specifications, the completed products used in packaging go through a number of development stages.
Among the requirements plastics must meet for packaging applications are higher wear and tear resistance, excellent durability, and extending the shelf life of food products. The medical and automotive industries, in particular, contain enormous potential for injection-molded plastics.
The sector for medical devices and components is predicted to grow at the fastest rate in the market. Demand for the product in the medical sector is anticipated to be driven by factors like optical clarity, biocompatibility, and cost-effective manufacturing.
Market Potential Of Plastic Injection Moulding
Injection-moulded plastics were valued at USD 284.7 billion globally in 2021. During the projection period, it is anticipated to rise at a compound annual growth rate (CAGR) of 4.2%.
The market is expected to be driven by the rising demand for plastic components from a variety of end-use sectors, including automotive, packaging, household appliances, electrical & electronics, and medical devices. The importance of injection-molded technology in the mass manufacturing of intricate plastic shapes has increased as a result of contemporary advancements to reduce the rate of defective production.
Over the course of the projection period, market expansion is anticipated to be constrained by volatile pricing of raw materials including benzene, ethylene, propylene, and styrene as well as increased disposal-related issues.
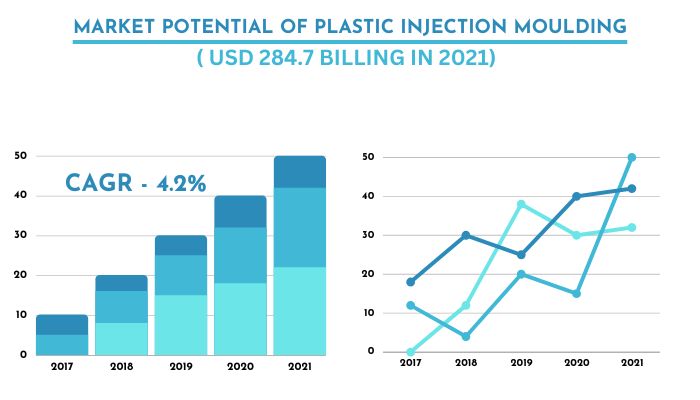
Businesses focus on producing injection-molded plastics using bio-based alternatives to address these problems. Rising construction spending is expected to fuel product demand, particularly in emerging economies including Brazil, China, India, Mexico, Russia, and South Africa.
The adaptive characteristics of the completed goods, such as their enhanced heat and pressure resistance, increase their utility in a number of industries. Government support in the form of tax exemptions and financial incentives to increase the flow of foreign direct investments has assisted the growth of the plastics industry in China and India (FDI).
They also provide inexpensive labour, which further lowers the businessesโ overall manufacturing costs. However, this change has led to the overproduction of certain plastic goods, which has an impact on their costs. However, a reduction in the consumption of injection moulding plastics has significantly impacted its demand in numerous applications around the world. Manufacturing activities have been slowed or stopped to stop the spread of the coronavirus.