Project Report For Iron Foundry
Introduction
Project Report For Iron Foundry is as follows:
A foundry is a metal casting manufacturing facility. Metals are cast into shapes by melting them into a liquid, pouring the metal into a mold, then removing the mold material once the metal has set as it cools. Aluminum and cast iron are the two most frequent metals treated. Other metals used in foundries to make castings include bronze, brass, steel, magnesium, and zinc. Parts of varying forms and sizes can be created during this procedure.
Foundries are a major contributor to the manufacturing recycling movement, melting and recasting millions of tons of waste metal each year to create new long-lasting commodities. Furthermore, several foundries employ sand in the molding process. Sand is another type of recycling that these foundries frequently use, recondition, and reuse.
To fully understand a foundry, one has to understand the casting process. Patternmaking, molding, melting, pouring, ejection, cleaning, fettling, and inspection are the general steps in casting. Because the final casting shape correlates with the mold it is poured into, molds are carefully molded with a pattern – a wood or metal replica of the thing to be cast. The most common mold material is silica sand, however they can be made from a variety of materials depending on the casting metal and procedure employed. A melting furnace is “charged” with metal and heated above the melting point of the metal.
The molten metal is tapped from the furnace into a refractory lined steel pouring ladle via a spout once it has reached a specific pouring temperature. The surface of the molten metal is scraped clean of slag and impurities. The ladle is then turned so that molten metal will pour into the mold’s cavity.
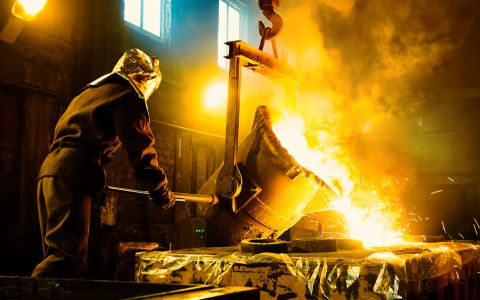
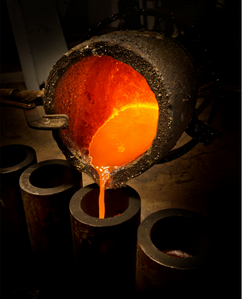
Benefits Of Iron Casting
Reduced Size Restrictions: The shape and size of the product are determined by the mold. In general, there are no restrictions on the size of the mold. The maximum load capacity is limited by the working space provided by the mechanism during cutting, whereas casting offers greater flexibility in withstanding larger loads at once.
One-piece Manufacturing: Casting is a one-piece manufacturing process. It does not merge numerous elements to create a single product. It’s finished when the molten liquid solidifies. The one-piece result is what makes casting items more solid and durable for the applications in question. Such as, for example, automotive components, which require welding to join separate parts together. In comparison, the same outcome can be obtained by pre-fabricating the mold to be the final product form and then casting.
Alloy Properties That Have Been Strengthened: Casting works with both ferrous and nonferrous materials, combining the qualities of all the constituents in the material. In some circumstances, one element is plastic but not thermally conductive. When it is combined with another heat conducting element, the alloy’s characteristics are enhanced.
Economy: Molds used in the casting process are frequently reusable, which means they can be used repeatedly until they are completely worn. When compared to cutting, which uses electricity while the machines are running, casting does not. In other words, the reusability and lower electricity use make casting a more cost-effective way of product creation.
Get Completely Custom Bankable Project Report
Market Potential Of Iron Foundry
The Global Iron Casting Market is estimated at USD 10.2 billion in 2022 and is expected to reach USD 15.13 billion by 2030, growing at a 5.8% CAGR (Compound Annual Growth Rate) between 2023 and 2030.
The global iron casting market has risen significantly in recent years, driven by demand from diverse industries such as automotive, construction, and industrial machines. The increasing demand for iron-casting products is attributed to their great strength, durability, and cost-effectiveness. We predict that gray cast iron will account for more than 64% of total sales in the Iron Casting Market. Gray cast iron is a low-cost alternative to other types of iron and metal alloys, making it a popular choice for a wide range of applications.
Iron castings are widely used in the automotive sector, where they are used to manufacture engine blocks, cylinder heads, and brake systems, among other things. The worldwide automotive sector has developed significantly in recent years, thanks to rising disposable income, a growing population, and urbanization. This expansion is projected to continue, boosting demand for iron castings in the automotive industry.