Project Report For Laser Cutter Machine
Introduction
Project Report For Laser Cutter Machine is as follows.
A laser cutter is a CNC (Computer Numerical Controlled) machine, which means it is controlled by a computer. A maker can develop their ideas on digital software and send them to the laser cutter to be cut. The laser cutter uses a laser beam to cut or etch into the material on the cutting bed after receiving the file. Laser cutters are an excellent all-purpose instrument since they can be used to create a variety of designs. Common laser cutters are primarily used to cut materials such as wood, acrylic, cardboard, paper, and so on.
A laser cutter is frequently used in engineering for precise cutting of machine components. A laser cutting machine is frequently used in industrial applications to cut structural and pipe components, as well as flat sheet material such as metal. The CNC settings may also be modified to etch or engrave any design on metal, wood, or plastic. Special CAD (computer aided design) software is used to programme the CNC and instruct it to accomplish the laser cutting project’s cutting, engraving, or etching specifications. The laser cutting machine’s size and capability decide whether it may be utilised for small or large-scale industrial tasks.
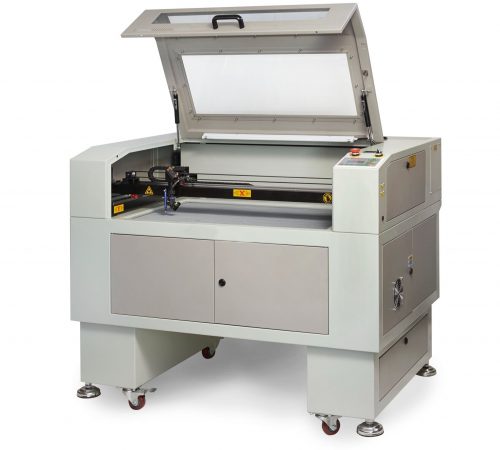
Types Of Laser Cutter Machine
CO2 Laser Cutter :- CO2 laser cutters are gas lasers that use carbon dioxide as the active laser medium. Because of their great power output capability and efficiency, they are the most prevalent type of laser cutter. CO2 laser cutters may generate up to 15 kW of power and have up to 30% efficiency (the highest of any gas laser cutter). They are particularly effective for cutting delicate features and acute angles in sheet metals or metals less than 10 mm thick. On thicker metal surfaces, higher powered CO2 laser cutters can also offer good cut quality.
Fiber Laser Cutter :- Fibre laser cutters are a more current laser technology that generates a beam from a bank of diodes and directs it through a fiber-optic cable. When cutting materials with a thickness of less than 5 mm, fibre laser cutters are faster and cleaner than CO2 laser cutters. Silver absorbs laser heat and begins to deform during cutting processes, making it difficult to get the desired machined component.
Crystal Laser Cutter :- CNC crystal laser cutters utilise beams composed of crystals such as neodymium-doped yttrium aluminium garnet and neodymium-doped yttrium ortho-vanadate. Crystal laser cutters often have greater intensity (or laser power) than CO2 laser cutters, allowing them to cut through thicker metals. These cutters can also cut metals, glass, wood, and plastics.
Project Report Sample On
Laser Cutter Machine
Get Completely Custom Bankable Project Report
Market Potential Of Laser Cutter Machine
The global laser cutting machines market was valued at USD 6,832.8 billion in 2022, and it is expected to grow at a 5.5% CAGR from 2023 to 2030.
The increased production requirements in numerous industries, as well as the necessity to eliminate human participation in metal processing quality, boost the demand for automation in manufacturing industries. These specifications are met by laser cutting equipment.
Growth in markets requiring laser cutting machines, as well as an increase in the need for automation in the industrial industry, are key influencing factors. Along with these aspects, the development of new technology for enhancing machines has an impact on the market. The previously mentioned aspect presents chances for market growth, however issues such as the availability of substitute machinery and the high cost of R&D hinder market growth. Nonetheless, each component is projected to have an impact on the market during the projection period.
The increasing adoption of industry 4.0 technologies such as automation, data analytics, and the Internet of Things (IoT) is assisting in maximising the efficiency of laser cutting machinery due to real-time information exchange that enables optimum output by enabling operators to monitor and manage their production processes. Manufacturers strive to reduce operating costs, reduce downtime, and increase output.