Project Report For Steel Castings
Introduction
Project report for steel castings is as follows.
Steel is an iron and carbon alloy. Steel is defined as having less than 2% carbon, while cast iron is defined as having more carbon. When cast irons are unable to provide enough strength or shock resistance, steel castings are employed. Low, medium, and high carbon steels are the different grades of carbon steel. The microstructure of steel varies depending on the carbon concentration. Controlling molten metal cooling rates and heat treatment can further improve this.
The goal of this project is to increase the value of steel castings by improving their precision casting, microstructure, and mechanical qualities. This will be accomplished by keeping an eye on and implementing best practises for moulding process control, melt preparation, and alloy addition as needed.
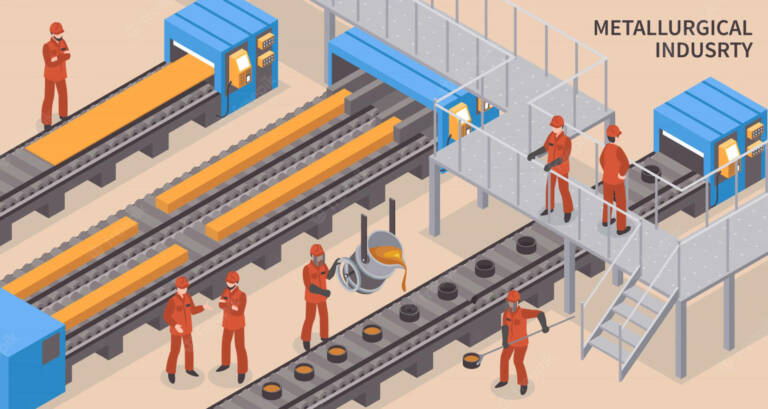
Product & Application of Steel Castings
Steel melts with good composition can be cast by melting in a medium frequency induction furnace. In addition to minimising the amount of carbon impurities, certain alloy components are added. Steel casting quality is ensured by a professional process control system. Alloys including manganese, silicon, chromium, nickel, vanadium, molybdenum, and other elements must be added to steel castings in order to get the desired end-use properties. In terms of heat, corrosion, and wear resistance, for example. Furthermore, for very high-end applications, most machines employ stainless and tool steels.
Critical components are frequently cast in steel for usage in a variety of industries. Critical machines like hydroelectric turbine wheels, forging presses, gears, railroad truck frames, valve bodies, pump casings, mining equipment, maritime equipment, turbocharger turbines, and engine cylinder blocks frequently make use of steel castings.
Sample Project Report Of Steel Castings For Bank Loan
Get Completely Custom Bankable Project Report
Raw Material of Steel Castings
Steels, including stainless steel, heat-resistant steel, corrosion-resistant steel, tool steel, and even high-speed steel, make up the raw materials. Assorted scrap steel or ingots for melting serve as the primary raw material. Fluxes, micro alloying additives, and ferro alloy components are additional ingredients. Molding sand and materials for creating patterns are additional consumables. certain moulding ingredients, such as graphite and refractory powder. Additionally, melt additives for cleaning and metal composition control are employed to obtain the appropriate casting quality and finish.
Market potential
Lorem ipsum dolor sit amet, consectetur adipiscing elit. Ut elit tellus, luctus nec ullamcorper mattis, pulvinar dapibus leo.
Expenses
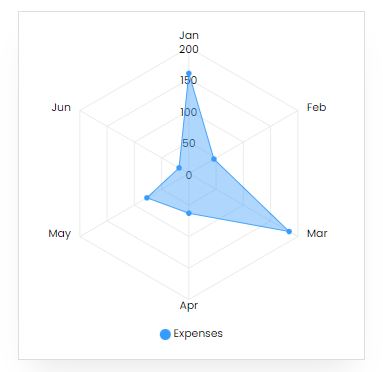
Product Cost Breakup
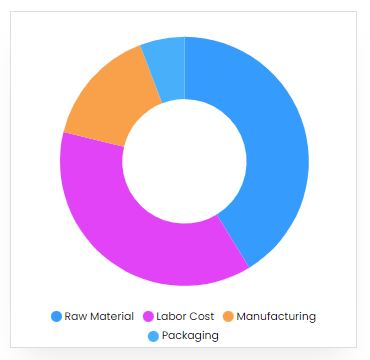
Reveneue Vs Expenses
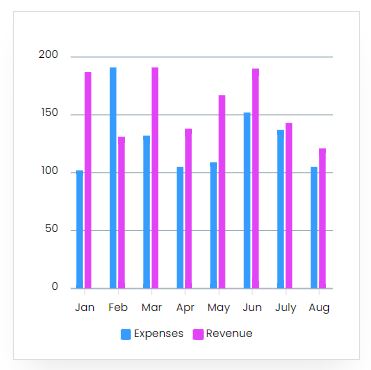
Market Trend
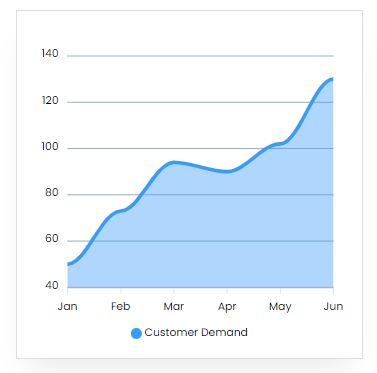
India is the third-largest casting maker in the world, behind China and the United States. India manufactures 11 to 12 million tonnes of castings annually. There are numerous big, medium, and small steel foundries in India that make cast items out of super alloys, stainless steel, and carbon steel alloys.
The majority of domestic and export requirements for the auto, mining, power, capital goods, railways, and defence industries are met by large companies. Electro steel Castings Ltd., Lanco Industries, Rail Wheel Factory, Hinduja Foundries, Nelcast Ltd., Tata Motors, Brakes India, Dcm Engineering Products, Sakthi Auto Component Ltd., Cooper Foundry, Mahindra- Hinoday, Mahindra Auto, Jayaswals Neco Ltd., NECO Castings, Ashok Iron Works, Kirloskar Ferrous Industries Ltd., Welcast Steels Ltd., etc. compete with various medium and small.