Project Report For Valve Manufacturing
IntroductionÂ
The project report for Valve Manufacturing is as follows.
A valve is a machine or natural object that directs or regulates the flow of a fluid (gases, liquids, fluidized solids, or slurries) by opening, closing, or partially obstructing different passages. Although technically fittings, valves are typically regarded as a different category. Fluid flows through an open valve from higher pressure to a lower pressure direction. The word is derived from the Latin valva, which refers to the door’s moving component, and volvere, which means to turn or roll.
The oldest and most basic type of valve is a flap with a free hinge that swings down to block fluid (liquid or gas) movement in one direction but is pushed up by the flow itself when the flow is traveling in the other direction. A check valve, since it prevents or “checks” the flow in one direction, is what this is. Modern control valves can manage downstream flow or pressure and work with sophisticated automation systems.
Project Report Sample Of Valve
Manufacturing
Get Completely Custom Bankable Project Report
The pre-shaped design of the body is first cleaned before beginning the turning process. The turning process involves removing and cutting superfluous materials while using a lathe or turning machine. A pre-shaped body must be mounted on a machine and then twisted during the process. As the machine rapidly spins, the body is cut with a single cutter into the desired shape.Â
Additionally, it adds holes, grooves, and other features to the body’s surface. The various body parts are given plating metal in order to ensure complete and appropriate sealing. After construction, the body needs to be polished. Technicians must create threads in order to connect specific valves to other components or pipes.
The required widths and lengths must be achieved by trimming the materials. The materials are then initially heated to get them ready for forging. There are no burrs or additional materials present. After removal, the body is flashed to take the shape of the correct valve. It alters the size and geometry of the valve’s holes, threads, and grooves. The process is dictated by the design requirements provided by the client. The valve is treated with an acidic solution.
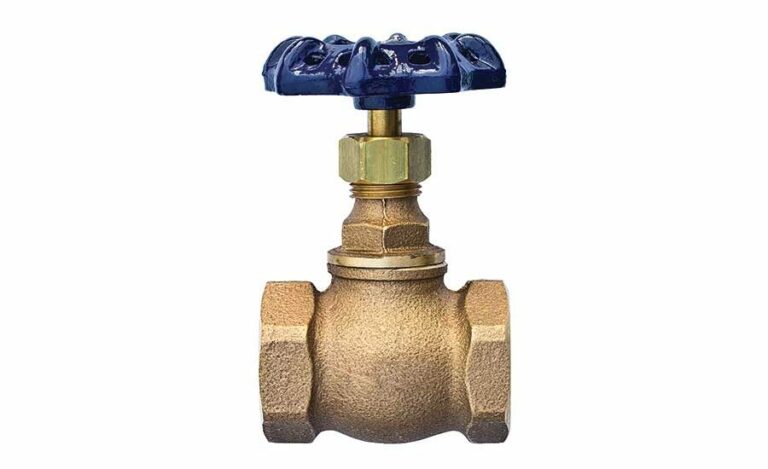
Advantage Of Valve Manufacturing
- They offer leak-proof service, are swift to open and close,
- They are much smaller in size than gate valves,
- They are lighter than gate valves,
- Gate or Globe valves lack multi-designed flexibility, which reduces the number of valves required.
- These valves are produced in a range of sizes and shapes to provide a flexible choice.
- High-quality valves offer safe operation under high temperatures and high-pressure situations, and they require less force to operate than conventional valves.
Market Potential Of Valve ManufacturingÂ
The market for industrial valves is anticipated to grow from $58,547.9 million in 2020 to $93,664.9 million in 2028, with a CAGR of 6.0 percent from 2021 to 2028. Industrial valves are used in the process sector to direct, regulate, and control gases, slurries, liquids, vapours, and other fluids.
Expenses
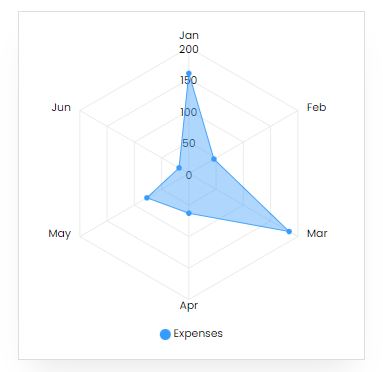
Product Cost Breakup
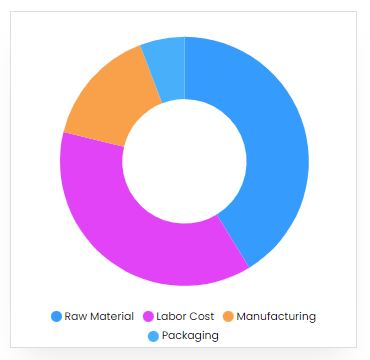
Reveneue Vs Expenses
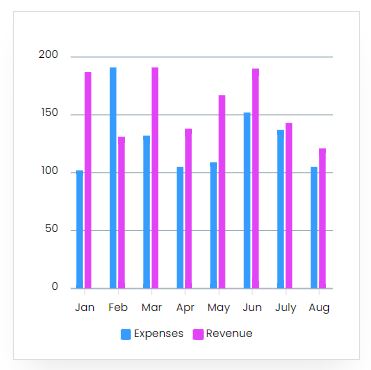
Market Trend
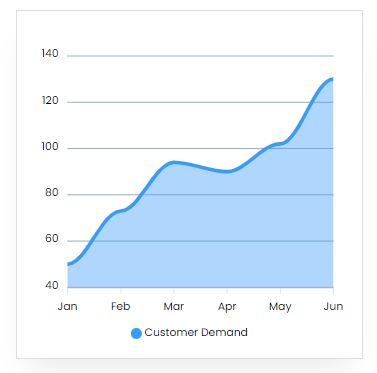
To provide effective flow management in sectors such as water and waste water, oil and power, food and beverages, chemicals, and others, industrial valves are mostly made of carbon steel, cast iron, stainless steel, and other high-functioning metal alloys.
A valve also comprises of a main body, a stem, and a seat, which are made of various materials such as polymers, rubber, metals, and others to prevent liquid from passing through the valve being wasted. The functioning mechanics of valves are what set them apart. Globe valves, butterfly valves, ball valves, gate valves, plug valves, pinch valves, diaphragm valves, and check valves are the most often used valves in industries.
Because of the increased emphasis on accurate placement and automation of industrial valves, automation in control valves has advanced significantly. A valve positioner, which transforms electrical impulses to pneumatic signals to operate the valve’s actuator, is used in control valves.
As a result, valve positioner automation provides greater efficiency, lower energy usage, and increased dependability, all of which contribute to the worldwide growth of the industrial valves market.
Furthermore, the oil and gas sector is the world’s largest user of industrial valves, with industrial valves being used in downstream, midstream, and upstream processes. Increased demand for industrial valves in North America increases the requirement for importing industrial valves from other nations, resulting in market expansion for industrial valves.Â
Furthermore, the food and beverage processing business in industrialised nations, such as the European Union, the United States, and China, is substantially saturated. The surge in food demand from emerging countries like Brazil, India, and others, on the other hand, supports the agriculture business, which in turn feeds the expansion of the food and beverage processing industry. This is also predicted to increase demand for industrial valves, hence promoting the industry’s growth.