Project Report For Warehouse construction
Introduction
Project report for Warehouse Construction is as follows.
The process of constructing a big, commercial facility meant to store commodities and materials for diverse uses is referred to as warehouse construction. Businesses, manufacturers, distributors, and retailers frequently use these facilities to efficiently store and manage their inventory. Location, design, materials, and functionality are all factors to consider while building a warehouse.
The initial stage in warehouse construction is to find a suitable location. For efficient operations, factors such as proximity to transportation networks, suppliers, and target markets are critical. The site should be large enough to support the intended facility, including parking, loading docks, and future development.
Warehouse design is critical for optimising space and workflow. Architects and engineers collaborate to design a layout that maximises storage capacity while minimising wasteful movement and increasing productivity. A thorough planning of aisles, shelving systems, racking, and storage units is required.
In addition, lighting, ventilation, and safety features are incorporated into the design. Materials used in warehouse building must be strong and long-lasting in order to sustain enormous weights and give long-term support. Steel is a common material for structural frameworks because of its strength, adaptability, and low cost. Concrete is a popular flooring material because it is strong and can resist the weight of forklifts, pallet jacks, and other heavy machinery.
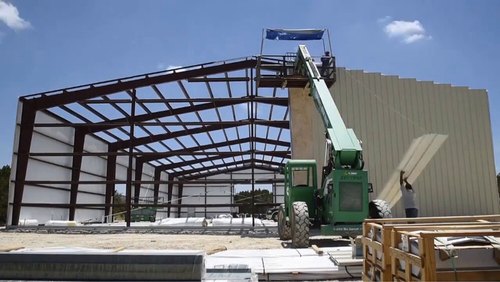
Types Of Warehouse Construction
Distribution Centres: These warehouses are strategically positioned to serve as hubs for transporting commodities to various places. They frequently have wide loading docks, large storage facilities, and efficient logistical systems to handle large volumes of cargo.
Cold Storage Warehouses: These facilities are meant to keep perishable items, such as food, medications, and flowers, at controlled temperatures. To keep the quality and freshness of the kept commodities, they require specialised insulation, refrigeration equipment, and humidity control.
Manufacturing Warehouses: These warehouses are integrated with manufacturing facilities to streamline production and storage processes. They are built to accommodate assembly lines, machines, and raw material storage, allowing for smooth coordination between manufacturing and inventory management.
E-commerce Fulfilment Centres: As online shopping has grown in popularity, e-commerce fulfilment centres have grown in importance. They are designed for quick order processing, inventory management, and order fulfillment. These warehouses frequently use automation technology, such as conveyor systems and robotics, to speed up the order picking and shipping processes.
High-Stack Warehouses: These warehouses are designed to maximise vertical storage capacity by utilising high stacking technologies such as automated vertical lift modules (VLMs) or high-density racking systems. They are ideal for keeping small parts, components, or goods with a rapid turnover rate.
Market Potential Of Warehouse Construction
In 2022, the size of the Indian warehousing market was INR 1,248 billion. The market is anticipated to develop at a compound annual growth rate (CAGR) of 11.5% from 2023 to 2028.
The market potential for warehouse building in 2023 is predicted to be solid and attractive. Several things contribute to this optimistic view. First, the fast expansion of online retail continues to generate demand for modern, efficient warehouses. As more people buy online, businesses are attempting to build or improve their e-commerce fulfillment capabilities, fueling the demand for cutting-edge distribution and fulfilment centres.
The evolution of supply chain management practises emphasises effective inventory management and just-in-time delivery. Companies must invest in strategically positioned warehouses to optimise their logistics operations, cut transportation costs, and increase order fulfilment times. As a result, there is a growing need for new warehouse construction as well as the extension and restoration of existing facilities.
Warehouse construction must be functional. The facility should be constructed to meet the specific demands of the business, such as the sort of goods being stored and the methods of handling and retrieval. Temperature control, security systems, fire suppression, and accessibility for loading and unloading are all carefully examined during the construction process.
Several stakeholders are involved in warehouse building, including general contractors, architects, engineers, and subcontractors specialising in various trades. Project management is critical in managing these teams and assuring adherence to timetables, budget limits, and building codes.
Project Report Sample On Warehouse Construction
Need Help?
Create 100% Bankable Project Report