Detailed Report On
Tube Manufacturing
Tube manufacturing is the process of creating cylindrical hollow tubes from raw materials like metal or plastic. It involves shaping, welding, and finishing to produce tubes used in various industries for applications such as transportation, construction, and fluid transfer.
Introduction
Detailed Report on Tube Manufacturing is as follows.
Tube manufacturing is a critical industrial activity that involves the construction of cylindrical structures that are used in a range of industries. Construction, automotive, aerospace, energy, and manufacturing are all industries that use these tubes. Tubes are constructed from a range of materials, including metals, polymers, and composites, each of which is tailored to meet specific needs.
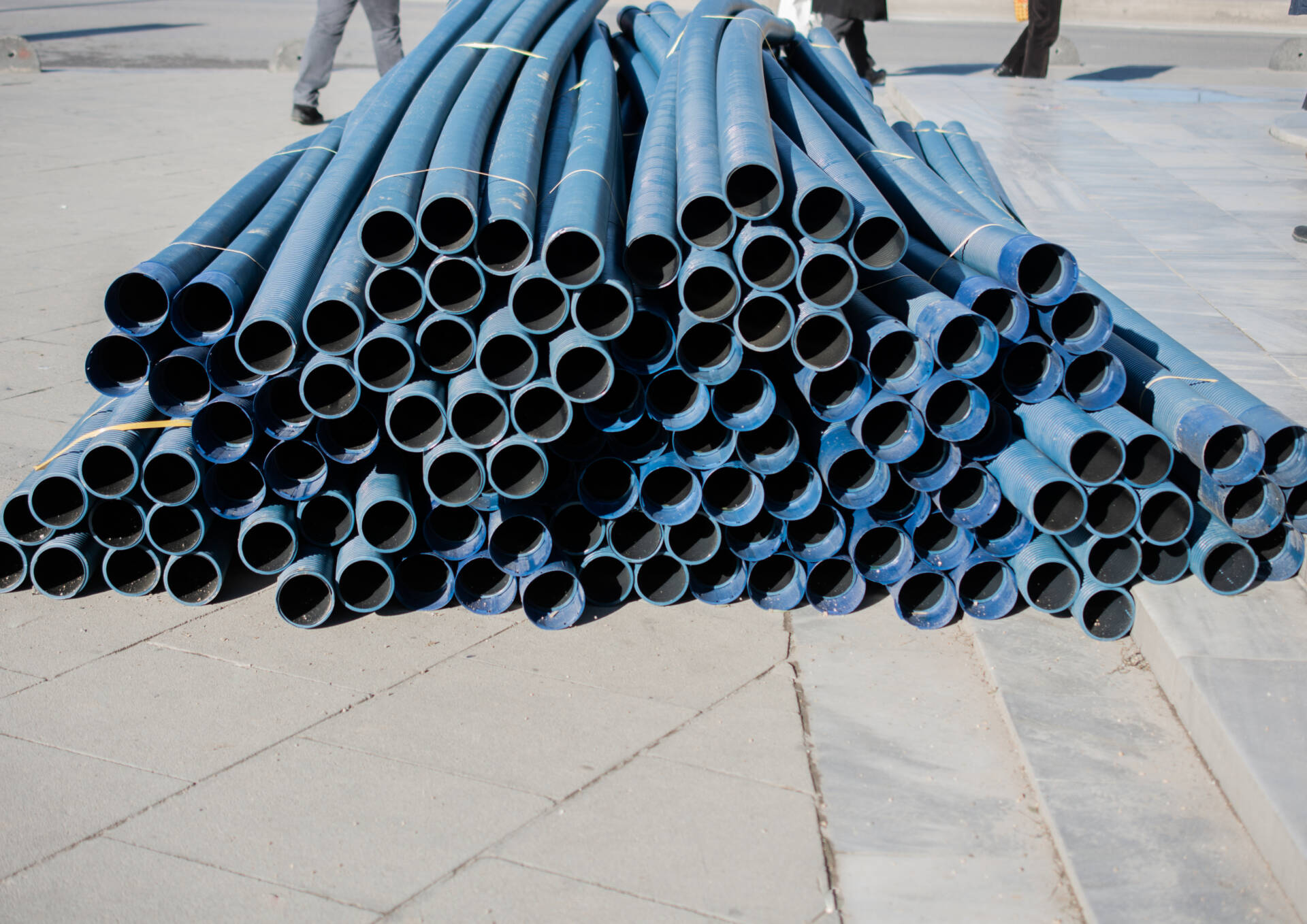
Tube manufacturing begins with the selection of suitable raw materials depending on criteria such as strength, durability, corrosion resistance, and needed features. Following the selection of materials, they are moulded into a tube-like shape using various shaping techniques such as extrusion, rolling, or casting. The material, as well as the needed dimensions and features of the finished product, dictate the procedure utilised.
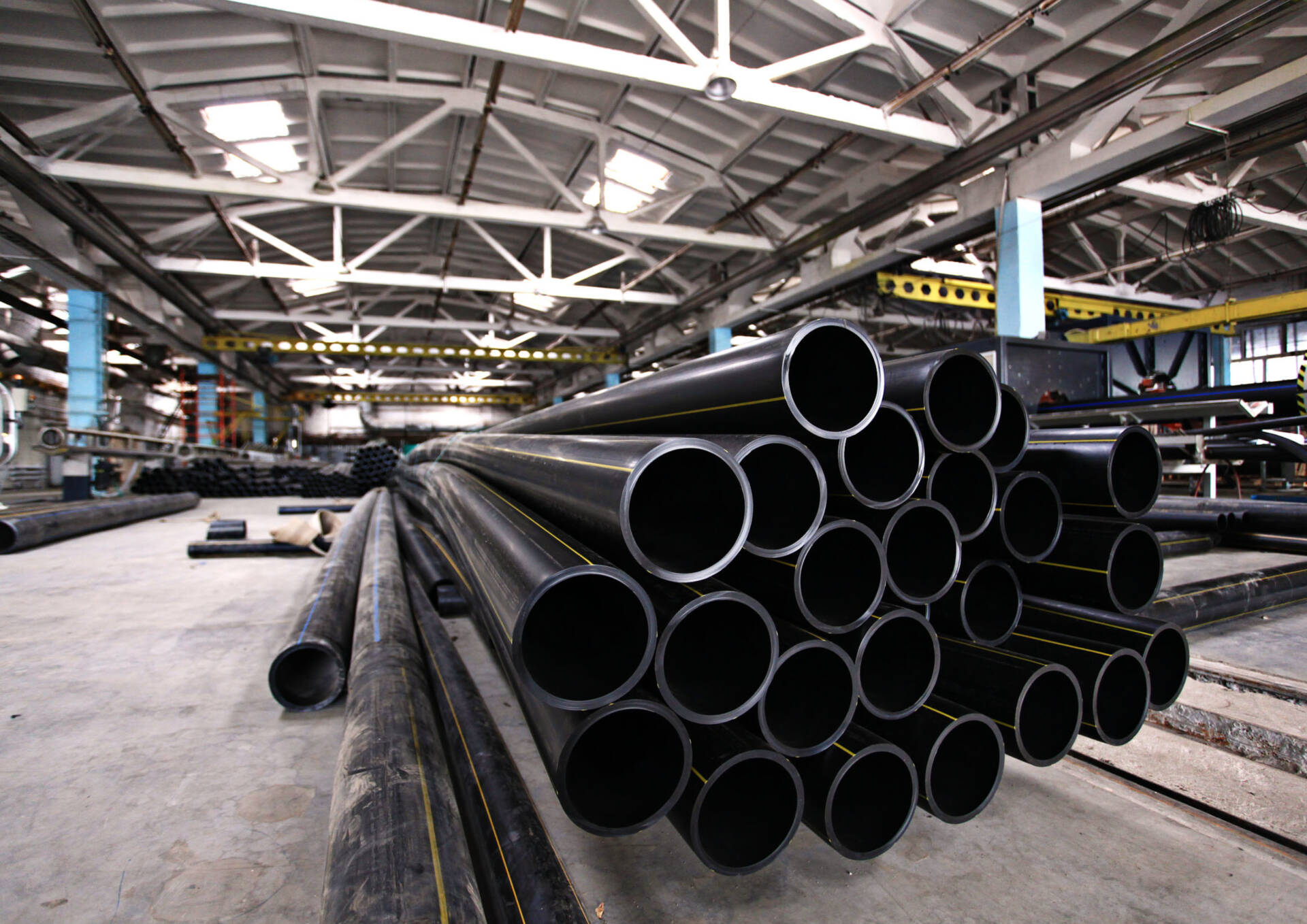
Following form, the tubes go through various processing procedures to improve their attributes. These stages could include heat treatment, cold working, or surface finishing procedures such as polishing, coating, or painting.
These treatments improve the mechanical strength, surface quality, and overall performance of the tubes. Quality control is a vital aspect of tube production since it guarantees that the finished products meet the stated specifications and standards. After passing the quality control inspections, the tubes are usually cut to the desired length, subjected to any necessary surface treatments, and then packaged and distributed.
Dimensional inspections, nondestructive testing, and material analysis are employed to assure the tubes’ integrity and quality. Tubes are frequently employed in a wide range of industries.
They’re used in building for structural support, plumbing, and HVAC systems. Tubes are utilised for fuel and exhaust systems, hydraulic and pneumatic lines, and structural components in the automotive and aerospace sectors. Tubes are used in the energy industry for transportation of oil and gas, power generation, and renewable energy applications.
Detailed Report Sample On Tube Manufacturing
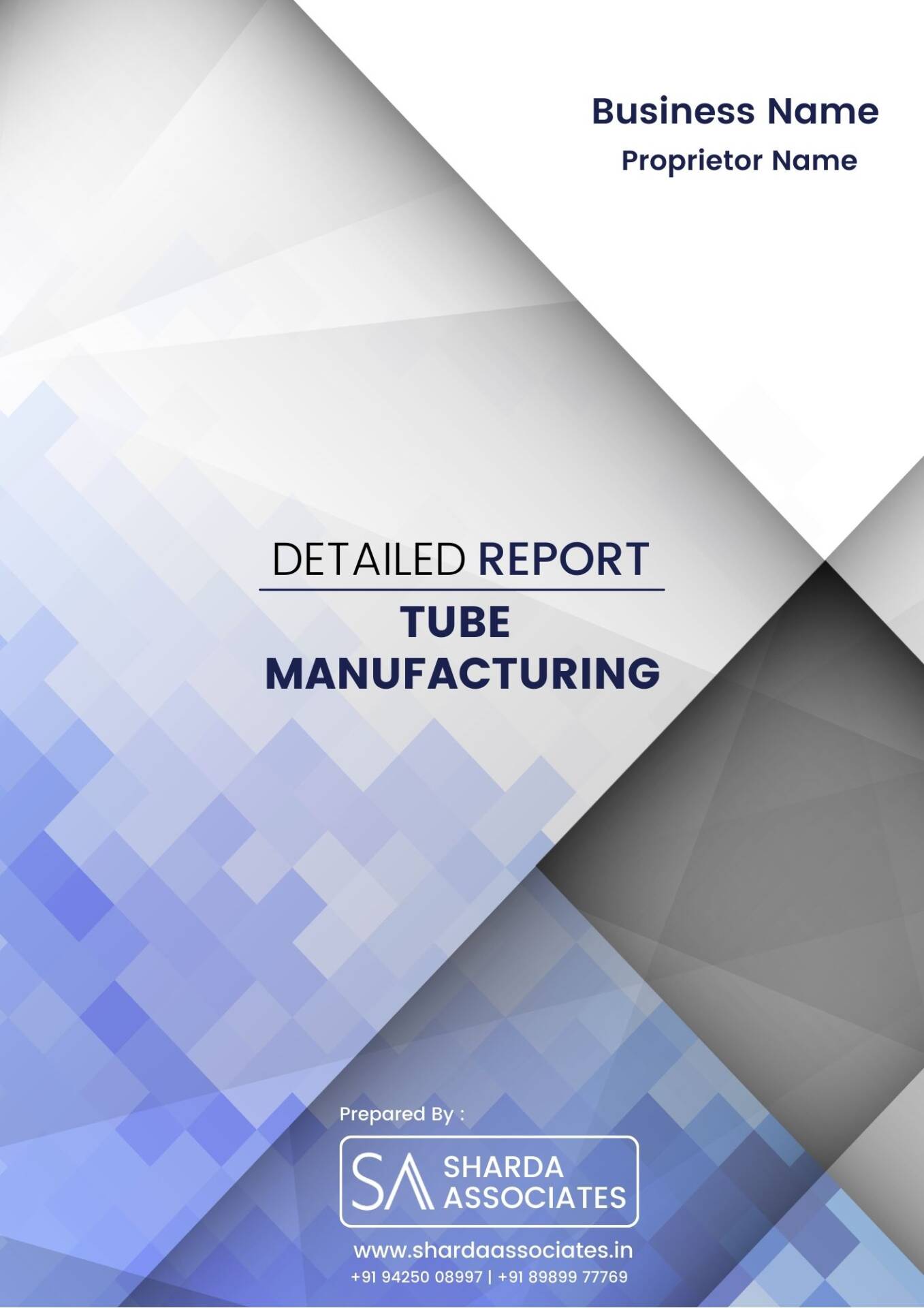
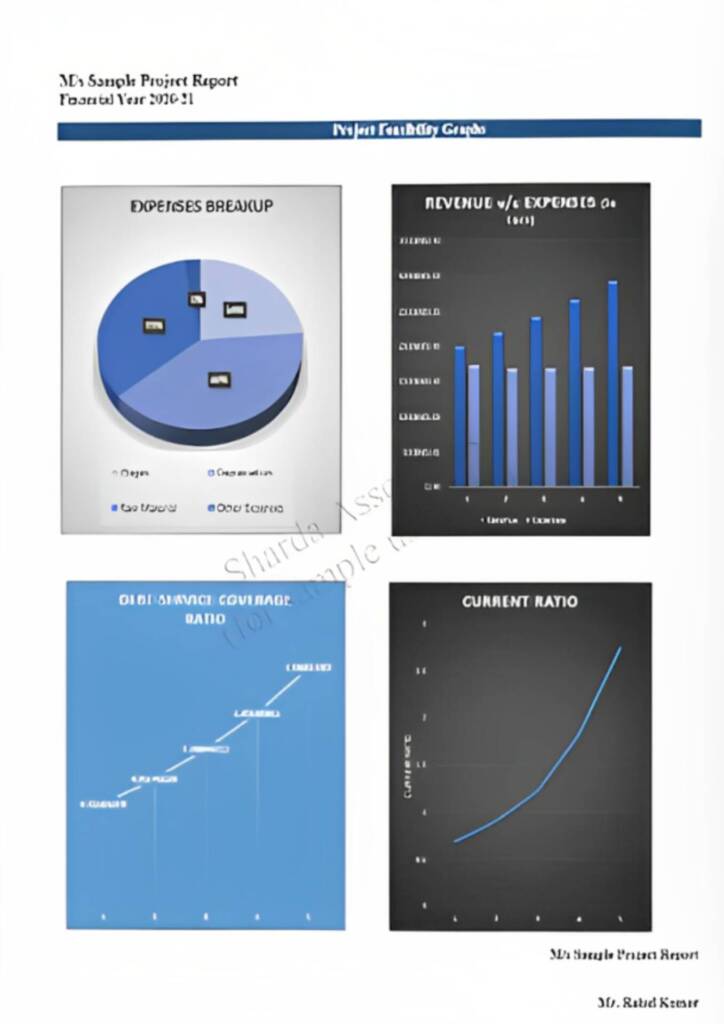
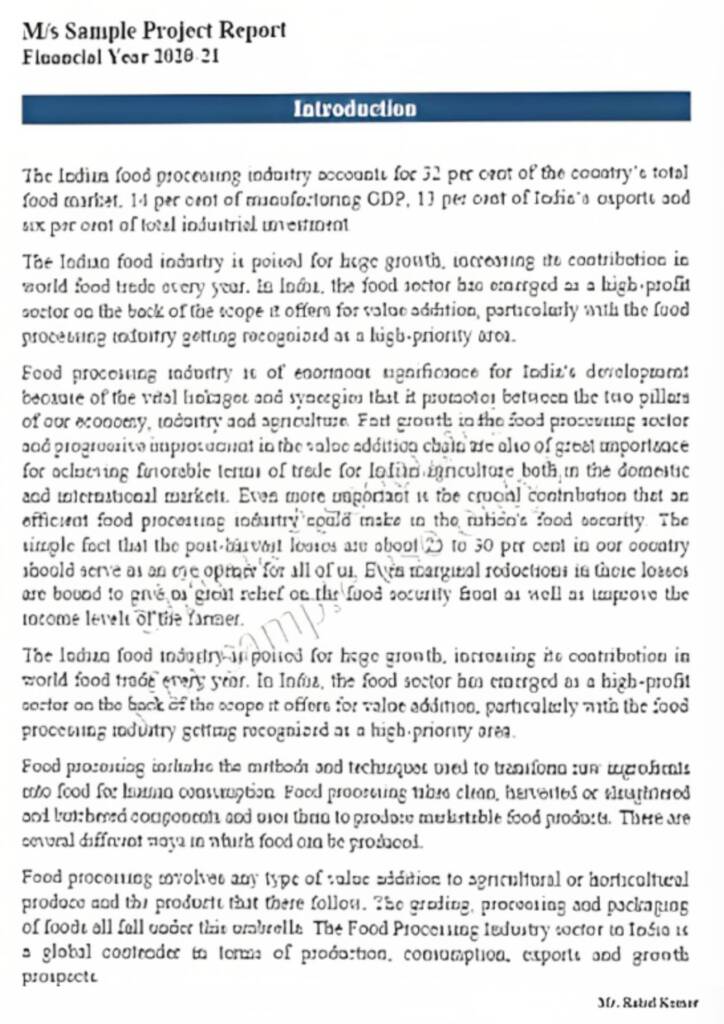
Market Potential Of Tube Manufacturing
The market for steel pipes and tubes, which was worth USD 142.4 billion in 2019, is predicted to grow at a CAGR of 6.2% between 2020 and 2027.
Rising demand for industrial tubes is a key factor driving market revenue growth in a variety of end-use sectors, including oil and gas (O&G), construction, and automotive. Manufacturers are focusing on developing creative and cutting-edge products as the demand for environmentally friendly and energy-efficient industrial tubes develops. Industrial tubes are hollow sections that are used in pressure equipment, mechanical applications, and instrumentation systems.
Industrial tubes are utilised in a variety of industries, including automotive, chemical, oil and gas, and petrochemical. Steel tubes for producing machine structures and their components are manufactured by key players in the Industrial Tubes Market using a broad variety of materials such as carbon steel and other steel alloys. The global demand for industrial tubes is expanding due to their varied qualities such as superior chemical and corrosion resistance, high strength, high durability, formability, and weldability.
They are available in round, square, rectangular, and oval designs. There are two types of industrial tubes: welded and seamless. Heat exchanger tubes, mechanical tubes, structural tubes, and hydraulic and instrumentation tubes are all examples of industrial tubes. The seamless tubes industry is predicted to dominate the worldwide industrial tube market. Because of its capacity to handle high pressure and extreme temperatures, these tubes are widely utilised in a variety of industries, including oil and gas, petrochemicals, and chemicals.
The seamless tubes are also very strong and durable, making them perfect for use in high-stress applications. The market expansion of seamless tubes can be attributed to rising demand for energy-efficient solutions as well as increased investment in the oil, gas, and petrochemical industries. Over the projected period, it is expected that the development of new oil and gas fields, as well as the increased use of unconventional energy sources, will raise demand for seamless tubes.
Contents of Project Report
A project report helps you identify whether a project is worth pursuing. It presents the holistic view and brings complete insight of the business and its activity.
It acts as a guide for all the business operations, aids in taking all financial decisions related to the existing businesses and to the start-ups. It serves as roadmap to the business and provides information to the outsider who are wanting to know more about the business.
You will have the opportunity to build new goals and expansion ideas in one single document. Everyone, from the banks to potential investors, will need to have a look at the project report before they shell out any money.
A well drafted project report generally consists details about:
- Brief History of the Business
- The Promoters
- SWOT Analysis
- Industry Outlook
- Past Financial Statements
- Projected Financial Statements
- Infrastructure and Human Resource required
- CMA data
- Business model
- Requirement of Working Capital Funds
- Means of Finance
Other relevant information, if any.