Project Report For Milk Chilling Plant
Introduction
Project Report For Milk Chilling Plant is as Follows.
A milk chilling plant, also known as a milk cooling plant, is a facility that quickly cools and stores fresh milk at a regulated temperature. A milk chilling plant’s objective is to preserve the freshness and quality of milk by inhibiting bacterial development and preserving its nutritional content. The collecting of milk from dairy farms is the first step in the process.
To reduce temperature changes, the milk is carried to the chilling facility in insulated tankers. When the milk arrives, it is promptly emptied into storage tanks within the factory. The raw milk is chilled by first putting it via a heat exchanger. This gadget rapidly cools milk by passing it via stainless steel plates or tubes. Cold water or a refrigerant is used to chill the milk, and the heat absorbed from the milk is dissipated.
The milk is chilled to roughly 4°C (39°F) or lower, depending on the region’s special norms and needs. This low temperature limits the formation of germs and helps to keep the milk fresh. After chilling, the milk is moved to insulated storage containers. These tanks are meant to keep the milk at a low temperature and keep outside pollutants out.
Agitators are installed in the tanks to guarantee equal cooling and to avoid the creation of cream layers or sedimentation. Milk chilling plants frequently contain testing and quality control capabilities in addition to cooling and storage. Milk samples may be obtained at various stages to look for anomalies such as excessive bacterial counts or adulteration. These quality assurance procedures ensure that only high-quality milk is processed or delivered.
Milk chilling facilities are critical components of the dairy industry, particularly in areas where milk is produced in considerable amounts. They are critical in preserving the quality and safety of milk, prolonging its shelf life, and permitting efficient milk collecting and distribution networks.
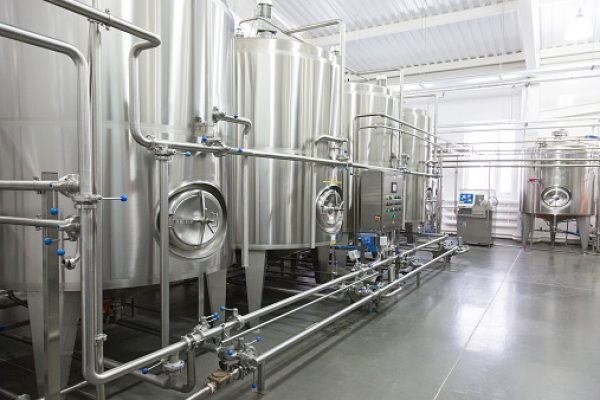
Types Of Milk Chilling Plant
Bulk Milk Cooling Tank: This is the most basic sort of milk chilling plant. It comprises of a single huge storage tank outfitted with cooling devices such as refrigeration units or direct expansion (DX) systems. It is appropriate for small-scale operations and is typically used on dairy farms or rural areas where milk is collected in bulk.
Instant Milk Chiller: Also known as a flash chiller, this type of plant is designed to swiftly cool milk to the necessary temperature within seconds. It employs a heat exchanger, which rapidly exchanges the heat from the milk with cool water or refrigerants. Instant milk chillers are often used in bigger dairy processing plants to provide effective chilling while maintaining milk quality.
Ice Bank Tank: Ice bank milk chillers employ a huge tank containing a refrigerant, often a glycol-water combination, which freezes to produce ice during off-peak hours when power prices are lower. The ice bank serves as a cold reservoir, and chilled milk is cycled through the ice bank tank to quickly cool. This sort of chilling facility uses less energy and is appropriate for larger-scale operations.
Market Potential Of Milk Chilling Plant
The market for milk storage cooling systems worldwide is anticipated to reach US$ 678.0 million in 2023. A sluggish 3.4% CAGR is anticipated to fuel market growth between 2023 and 2033. In 2033, this ought to generate US$ 947.1 million.
The generated raw milk must be chilled both before and after processing. Being very perishable by nature, milk must be protected against contamination at all costs. The primary raw ingredient for the dairy industry is milk. The majority of milk coolers’ structures are made of stainless steel. While some dairy farmers choose to own milk coolers, others might rent them from dairy facilities. Open tanks have capacities between 150 and 3000 litres, whereas closed tanks have capacities between 1000 and 10000 litres.
Dairy cooperative businesses are driven by the increasing production and consumption of milk both in urban and rural parts of the world. When it comes to the effective supply of high-quality milk, together with value-added goods and dairy commodities, the function of a milk tank cooling system becomes unavoidable.
Project Report Sample On Milk Chilling Plant
Need Help?
Create 100% Bankable Project Report